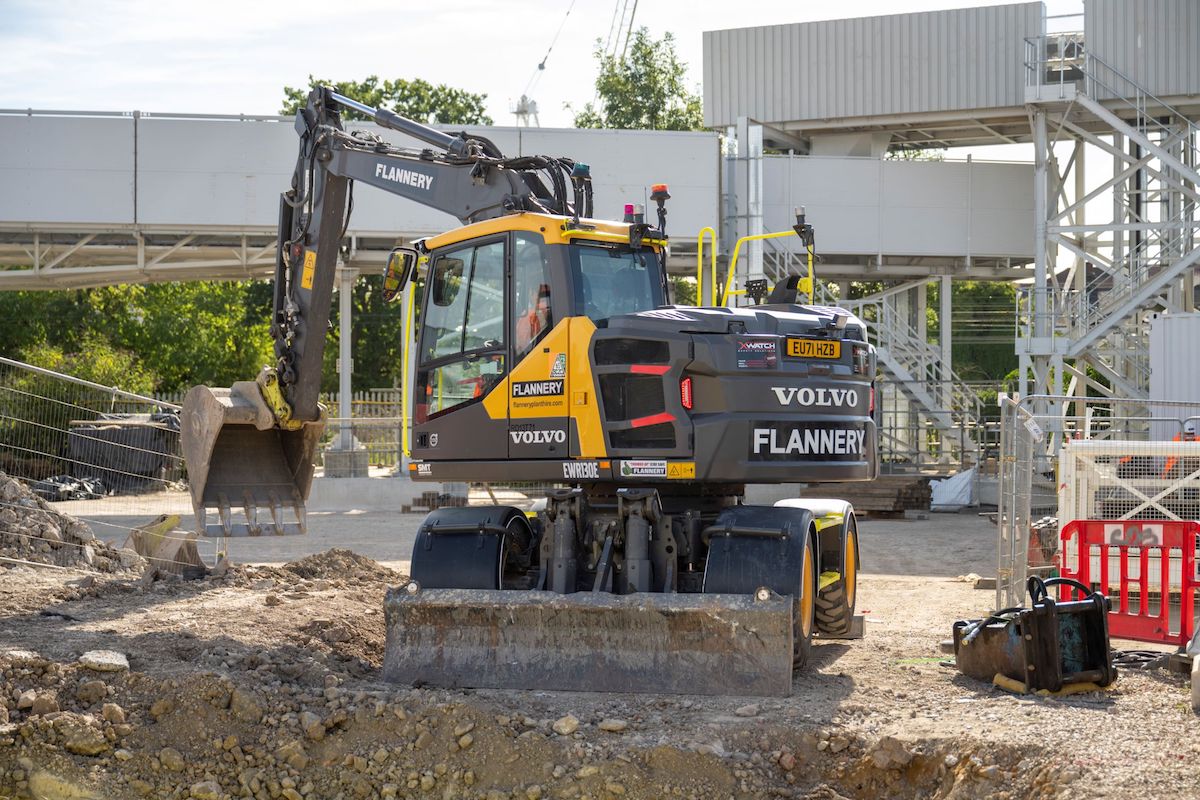
Technology and training go hand in hand for one of the UK’s major plant hire firms, when it comes to improving site safety. CPN reports.
The push for greater safety on the UK’s construction sites comes from both the plant hire companies themselves and from their customers. For a company like Flannery Plant Hire (FPH), which gets 80% of its business through tender, the issue of health and safety will be up there alongside price as one of the major qualifications.
Its answer has been to invest in sophisticated technology, complemented by a comprehensive training scheme for every level of the business — apprentices, qualified operators, and managers – through skills hubs operated in partnership with Balfour Beatty.
So, not only was FPH one of the first major plant hire companies to buy products from Xwatch Safety Solutions when it started back in 2019 but many of its customers specify the company’s products too. Kier Group, Balfour Beatty and Morgan Sindall, for instance, specify Xwatch XW4s and XW5s. Other customers specify the Xwatch 3D collision avoidance system, which integrates with the Leica MC1 3D machine control software and so enables users to create or import 3D avoidance zones above and below ground directly into the MC1 tablet without additional screens.
Upwards of 45% of Flannery’s fleet is equipped with Xwatch systems, including almost 300 XW4 height and slew control systems along with XW5 total protection RCIs (rated capacity indicators) – and there are more to come. “We have just purchased 75 Cat machines, all equipped with Xwatch,” says Ben Seabright, Flannery’s buying manager. “The user-friendly interface of Xwatch makes it easy for operators to adapt quickly and work more effectively.”
Flannery’s attitude toward safety in construction revolves around utilising all available tools to keep the operator, site personnel and the public safe. For example, on a road project, this would include height, slew, and full 3D avoidance to prevent machines from entering the carriageway, vastly improving site safety. Another example would be MoD facilities, which can be particularly complex, with diverse surroundings demanding various ‘tools’ for operators to focus on their tasks safely and effectively.
One challenge in modern construction machinery is in-cab clutter, where too many screens obscure the operator’s view. Lights and constant alarm tones can overwhelm operators, running the risk of becoming just background or white noise. Tasks in busy worksite environments demand intense concentration and strict personal safety rules—in-cab clutter risks distracting the operator, and the constant alarms may go unheard.
“Xwatch systems are designed to manage and control safety parameters actively,” says managing director Patrick Flannery. “This enables our operators to focus on the job at hand without being overwhelmed by excessive in-cab notifications.”
Flannery’s business model gives it a great deal of clout because everything can be planned in the medium term. Right now the company is working on projects that include the A3, M5 and M25 National Highways widening works at Wisley and HS2 which, as is usual practice, it tendered for between six and nine months ahead. This means that it can plan its purchases 12 months ahead.
Last year, for example, Flannery invested heavily in new machinery for upcoming key infrastructure projects. While the company has tapered its CAPEX this year, more than £105 million has already been committed for new machinery and equipment.
The result is that it can strike up partnerships with particular OEMs such as Cat, Komatsu, JCB, Volvo, Bomag and Wacker Neuson.
And it is the same when it comes to site safety systems, says Patrick Flannery. ”We choose our partners carefully, looking for those who share our ethos of delivering first-class service efficiently. This is why we collaborate with a select few OEMs and partners who can react quickly and ‘get it done’.”
So now it is partnering with Xwatch to simplify operations and improve productivity and safety by creating a streamlined, integrated system in which a single set of machinery controls incorporates all technological partnerships.
This initiative dovetails with Flannery’s three skills hubs. These are supported by companies such as SITECH/Trimble, Leica, and Xwatch and train its staff on the latest semi-autonomous machinery.
The skills hub has also launched its compliance plus program, focusing on operator competence, machine control familiarisation and eco-operation.
“All technology is contained within a ring-fenced site at the skills hub,” says Patrick Flannery. “This setup distinguishes us from other plant hire companies and allows us to quality assess and train operatives to a high standard required for the diverse nature of the work they will be required to undertake.”
Flannery’s far-sighted approach means that it has leveraged its purchasing power so that it has a strong input into the technology being developed and then recruited its suppliers – or partners – to develop the training required.