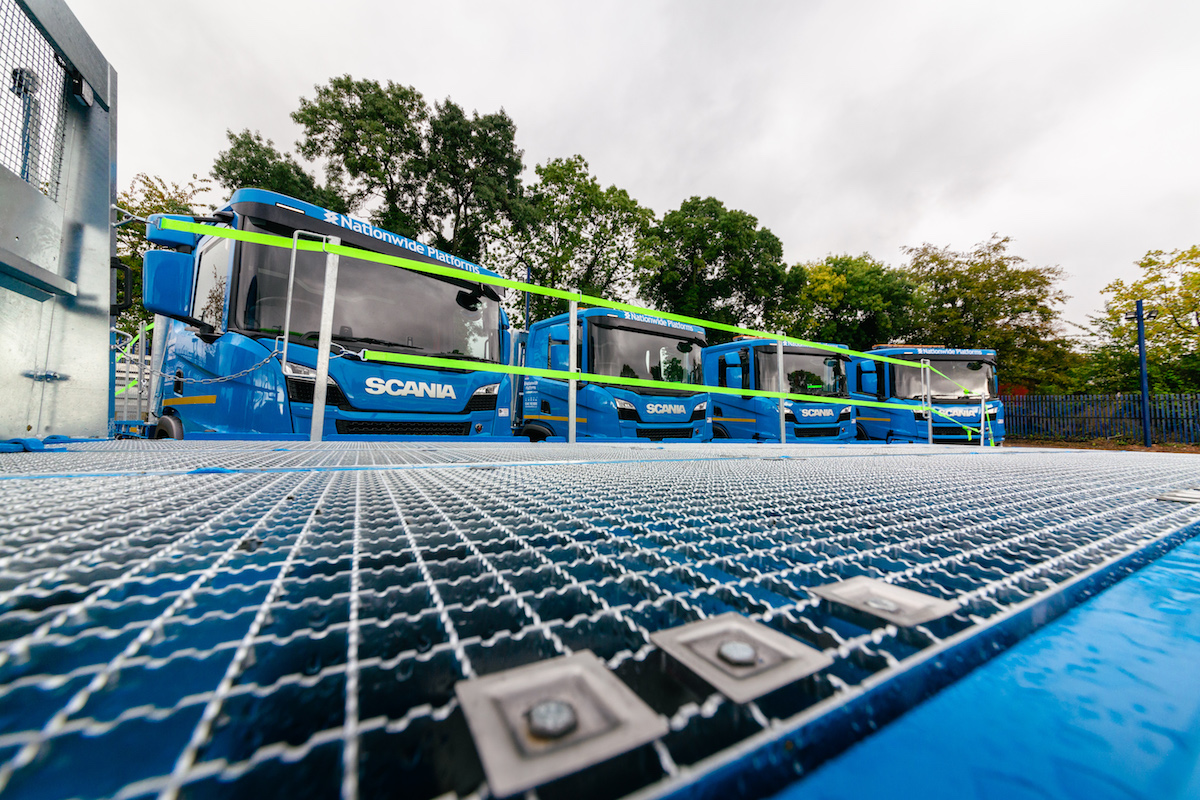
Need to move a bit of kit about but not sure what type of truck deck will be right for the job? Plant body builder Sterling is on hand to advise.
Okay, you already know that you want your mode of transport to be safe and durable enough to handle some tough situations but what materials should you choose?
Having designed and manufactured beavertail truck bodies for various sectors in the industry, we know that each has its own unique decking requirements. So, what factors should be taken into account to make the right decision?
The point-loading of the load is one of the most important considerations when choosing decking. While some trucks will transport a full load of small lighter kit per run, other trucks will transport less items which may be very heavy. Some machines, whilst they may be small have extremely high point loading, e.g., a road planer or 3-wheel forklift. Other machines such as large 14 tonne excavators haven’t necessarily got the highest point loading but tend to have the greatest mass.
Then there’s also the matter of the type of traffic to be accommodated. A truck body, its decking, and loading ramps will have to tolerate anything from steel tracks to rubber wheels and tracks to metal drum rollers. Rubber tracks and tyres would cause less stress on surfaces as the rubber is a softer material whereas steel tracks can even cause damage to some deck surfaces. Rollers with their smooth steel drums have little grip so again have their own unique decking requirements.
A good decking
There are basically four different types of decking for truck bodies, which can be configured in different combinations to meet the individual requirements of each operation. Each type of decking has certain characteristics which makes it suitable for each individual application.
Timber!
Timber decking is the most popular choice for truck decks; and the most popular type of wood used is Keruing, a Malaysian hardwood. It is long lasting and has an excellent strength to weight ratio. This tough wood has the same density as Red Oak, and twice the hardness rating of White Oak. The secret to its strength lies in the interlocking wood grain. This has a good point-loading strength, meaning it is great for most applications, particularly steel tracked vehicles and equipment with a high point loading.
Grate stuff
To improve grip, some clients prefer to use a heavy-duty steel grating instead of timber. This is material has its own inherent strength so isn’t required to be combined with other materials. The grip provided by this surface is particularly good for rubber tyres, but is not as suitable for steel tracks, and drum rollers. The grating is zinc galvanised prior to fitment, making it resistant to rust. This is a very popular option for access machinery hire firms as it is particularly handy when carrying scissor lifts, cherry pickers and spider-lifts.
Mesh it up
Steel expanded mesh is a great complementary product to the timber deck and is fitted atop of the timber to give fantastic grip. The mesh is galvanised and is usually used for trucks that have a variety of equipment transported on them, from rubber tracked diggers to road planers to scissor lifts. A good half-way house between the two surfaces outlined above.
Steel durbar
Steel durbar has extremely high impact strength and is used on decks that carry very heavy weights. As it can be very slippery, particularly when wet, it is typically confined to small areas of the deck that will be subjected to extreme point loading such as the area in the centre of the deck where the knuckle of 14-tonne excavators tend to sit. A deck option other than steel durbar plate in this application is at risk of damage.
Whilst deck type selection is important, it is just as crucial that the supporting frame beneath the deck is appropriately built. For example, the industry standard spacing between supporting cross-members is 400mm, but a Sterling build exceeds this specification by fitting the cross-members closer together at 300mm giving far greater point loading leading to vastly reduced deck wear.
In addition, commonly used box section cross-members are prone to rust meaning that over time, the deck support becomes compromised. The Sterling product is built using I-beam or C-section cross-members as all the ‘black’ steel on these can be fully paint protected meaning your deck will have sufficient underlying strength for a far greater period (often years) than alternative builds.
Sterling manufactures beavertail truck bodies and is based in North Yorkshire. It builds plant bodies for 14-32 tonne trucks, manufacturing over 230 beavertails in 2023. It has an extensive after sales service team throughout the UK.