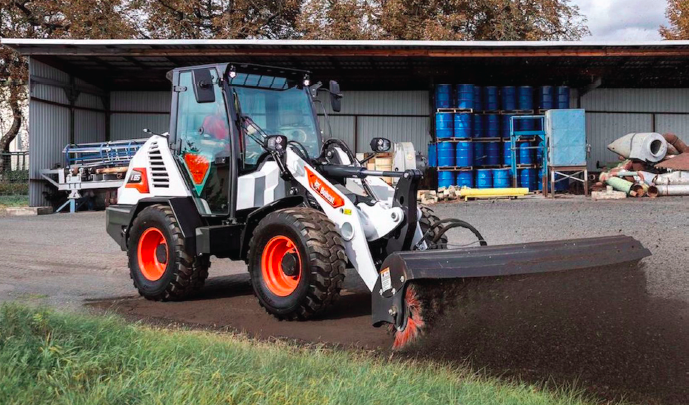
Attachments product manager, Katinka Kincses is responsible for product development, marketing, additional services and training.
“I view my department as the voice of the customer. We map out their wishes and conduct field research to develop new attachments and new functions. We have two important principles.
“The first is the fact that job sites are becoming smaller and that the demand for compact machines and compact attachments is increasing.
“In addition, ease of use is becoming increasingly important. Many companies are struggling with staff shortages, which means you need to offer alternatives to human labour.”
As a result, Bobcat’s machines and attachments are designed to be intuitive and user-friendly, ensuring that even young or inexperienced operators can work effectively with minimal training.
This focus on simplicity doesn’t come at the expense of productivity — advanced automation features help maintain efficiency. Take the modern grader, for instance: equipped with cutting-edge technology, it can perform many tasks almost autonomously, reducing the need for highly skilled operators while keeping output high.
Attachments are also vital to customers’ businesses, Kincses believes, enabling them to maximize the versatility and value of their machines. For most operators, she argues, investing in a multi-purpose tool carrier is a more practical choice than purchasing specialist equipment.
“A customer should only consider a specialist machine if they are performing the same task all day, every day,” she explains. “For example, a ride-on mower might be perfect for maintaining a golf course, but in most other cases, a multi-purpose tool carrier is the better investment. With the right attachments, you can take on more projects, work throughout the year, and make better use of your machine.”
She points to a common trend among new customers: “Often, they start with a machine and three or four attachments. As they realize how much more they can do, they gradually expand their collection, adding another three or four attachments over time. This approach allows them to adapt to different tasks and get the most out of their equipment.”
Yet customers cannot simply choose any compact machine and expect the attachments to compensate for mismatched capabilities. The machine itself must be suited to the core demands of the job, with attachments fine-tuning its versatility and efficiency.
“We supply one of the most extensive ranges of attachments, enabling operators to handle common tasks across construction, landscaping, agriculture, demolition, recycling, and material handling,” explains Kincses. In the current market attachments are vital to the success of most machines, particularly in the compact sector. At Bobcat, Katinka Kincses says what machines need which attachments, as she explains to Construction Plant News.
“However, selecting the right machine for the job remains crucial. Attachments enhance a machine’s capabilities, but they can’t fully compensate for choosing the wrong base machine.”
As she points out, the choice of machine should be tailored to the work environment and specific tasks. “For example, a skid-steer loader is strong and agile, making it ideal for firm ground. But on sensitive terrain where minimal soil disturbance is important, a compact track loader is a better choice. Similarly, power requirements must be considered. Heavy-duty tasks like using a forestry mulcher, wheel saw, or snowplow demand machines with high-powered hydraulics.”
“No one machine does it all,” Kincses says. “The key is matching the right machine to the task and equipping it with the right attachments.”
Bobcat’s attachment range spans multiple industries and includes everything from buckets and pallet forks to specialized tools like concrete mixers, tree transplanters, and graders. The range is also designed for compatibility, enabling attachments to work across different machines.
Ease of use is a priority in Bobcat’s design philosophy. The company’s Power Bob-Tach system, for instance, allows the operator to connect and disconnect non-hydraulicattachments without even leaving the cab. Another useful feature is the speed management system that allows the travel speed to be adjusted independently from the engine speed, allowing for higher productivity.
Then there is the attachment control device (ACD) built into the attachment. It is a CANbus system that controls the communication between the machine and the attachment. Thanks to the ACD, the machine recognises the attachment and automatically adjusts the settings of, among other things, the joystick controls and the hydraulics.
The driver can adjust the settings on the display in the machine and receive an overview of the operating hours, performance and status of the attachment. If an operator uses remote control to work their machine, all functions for controlling the attachment are also automatically available.
“For operators using remote controls, all the attachment functions are integrated and ready to use,” Kincses adds. “It’s about making everything as seamless as possible.” Kincses cautions against mixing and matching attachments from different manufacturers, emphasizing the importance of compatibility and reliability.
“By sticking with one manufacturer, you avoid situations where different suppliers blame each other, leaving you with unresolved problems. It’s also a matter of ensuring the machine and attachment are optimised for safety and performance.”
Looking to the future, Kincses promises that tomorrow’s attachments will reflect operators’ needs, continuing the trends that she has identified. “We’re working on attachments that address the challenges operators face today — compact solutions, more automation, and tools that make the job even easier.”