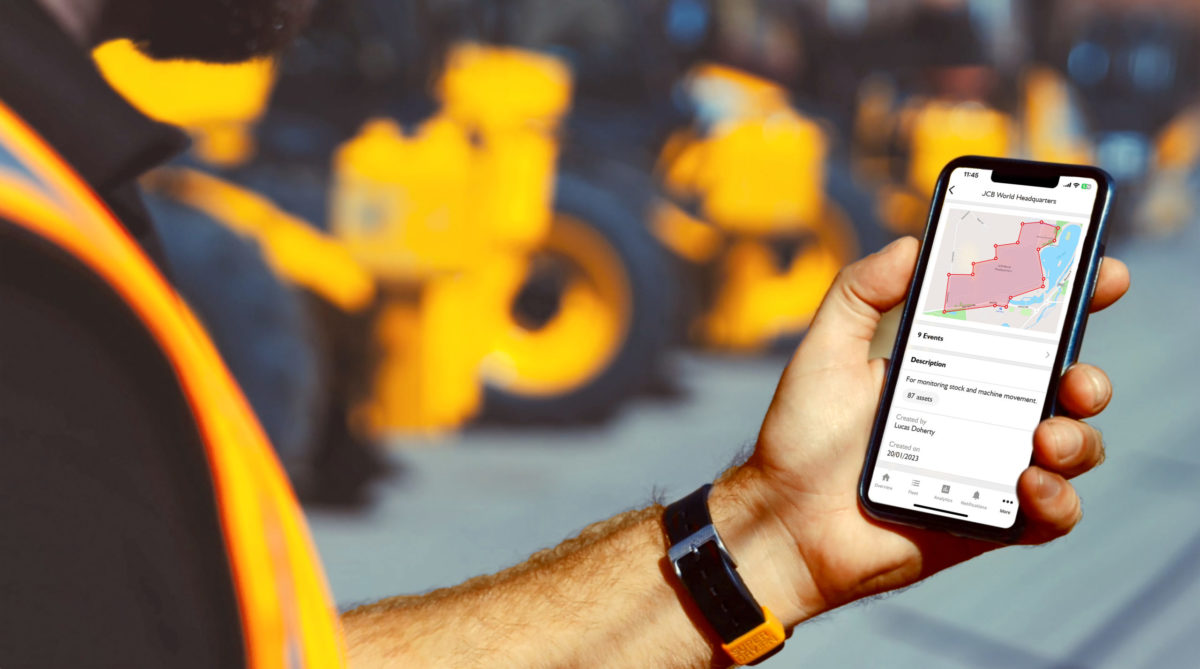
Construction Plant News visits JCB’s World Parts Centre, where the LiveLink system is making all the right connections
The JCB LiveLink journey began back in 2007. Today, someone logs into the telematics platform every 2.2 seconds with over 83,000 users globally, and more than 400,000 connected assets on any given day. “Rather than connecting to a machine, we’re connecting to a customer,” explains Tom Whitaker, General Manager of Product Support based at JCB’s expansive World Parts Centre. “And the guiding principle is an improved end user experience.”
The LiveLink team want JCB’s customers to be able to access quantifiable value from across their entire fleet, including the operators who own multiple brands. That’s why the system is designed to bring in data from other OEM machines – with more than 20 already integrated into one easily accessible portal. Not only that, but assets from product groups that JCB doesn’t even manufacture can be included too – such as welfare units, grading equipment, and even piling rigs.
LiveLink is an analytical tool that allows JCB users to increase their uptime, reduce admin in their business, minimise costs, increase safety and help them make better decisions about the management of their fleet. One of its key features, for example, is to alert customers when they need to take action, with all the alerts that an individual machine has issued viewable, as well as any documents that are stored against it. LiveLink is, in fact, a great storage mechanism for anything from LOLER certificates for lifting equipment to oil sampling data.
No two customers are the same, of course – nor indeed are individuals from the same organisations. Maintenance staff will be concerned about the health of the fleet, for instance, whilst safety managers might be looking at issues around improper usage. Alerts can, therefore, be customised to an individual’s own remit, ensuring that what is of most relevance is readily available.
So just what functionality is available? All of the information you would expect on a telematics platform is included, from service and maintenance, to hours, fuel usage and CO2 emissions. LiveLink users are increasingly focusing on utilisation data, ensuring that a piece of plant is not over or underutilised and could, for example, be moved to another project or off-hired.
Similarly, many contractors are now targeting idling as a means of reducing both fuel costs and CO2 output and LiveLink can supply that data for individual machines or across the whole fleet. Indeed, JCB’s telematics solution can form a key pillar around which a contractor or hirer can build a sustainability strategy. The cost of fuel, based on usage across a single day or any given time period, can be interrogated, for instance, and the potential for savings are huge, especially when taking into account the end of the red diesel rebate. The numbers can then be compared across sites, projects, product groups, or regions, allowing trends to be identified. “The vision is to measure the ‘as planned project’ with the ‘as built’”, continues Tom. “’Did we use more fuel than anticipated and why?’ If the answer to that is yes, then LiveLink can facilitate an intervention at a much earlier stage of the build schedule protecting what are often very fine profit margins.”
Contractors can also gain further insight through a LiveLink rental feature that enables hirers to share visibility of a machine for a period of time with the end client. As a result, builders can see machines within their own LiveLink system that are actually owned by the hirer. In the same way, construction companies working as part of large joint venture infrastructure project can share information on machinery each party owns.
Telematics remains a vital weapon in the fight against theft, which makes geofences and curfews vital security features, whilst geofencing has equally taken on a further site efficiency role in recent years. When a machine has left or entered an area that then acts as a trigger for some form of activity to take place. A further location-based advance has arrived recently with the integration of what3words. The system splits the entire planet into 3m x 3m sections, each of which is given a unique three-word code to describe it, which won’t be used anywhere else in that combination.
With JCB machines often operating in remote locations it means the exact location can be identified without the use of a complex longitude and latitude number reference. It’s then issued to maintenance and service personnel, or delivery drivers and, when accessing LiveLink on an Android and IOS app, directions can be immediately fed into Google or Apple Maps.
Moreover, JCB LiveLink is integrated with the manufacturer’s standard operator app. This allows a customer to set configurable daily checks on an asset, which can be set at the level of an entire organisation, product group – such as excavators or telehandlers – or on an individual site, thereby digitising processes that have too often been paper-based. Operators can access key documents, and complete daily checks and, when one of these is not undertaken, the responsible individual can be alerted.
JCB’s Customer Uptime Case Management System is a support module within LiveLink that enables a customer to request help with a machine from their local dealer. A customer can create a case, adding details of what’s wrong, with pictures or video to improve first time fix rates. Live updates of the repair status as it progresses can then be viewed, and when it’s been completed. The result is complete transparency, from when the engineer is setting off, to awaiting parts.
“The end game is an eco-system where the right people get the right information in an easily digestible format,” concludes Tom. “The demise of red diesel, the rising cost of fuel, and the scarcity of labour has increased the added value of telematics incrementally, and the willingness of our customers to engage with it has expanded in parallel.”
For further information on JCB’s LiveLink Telematics system visit www.jcblivelink.com