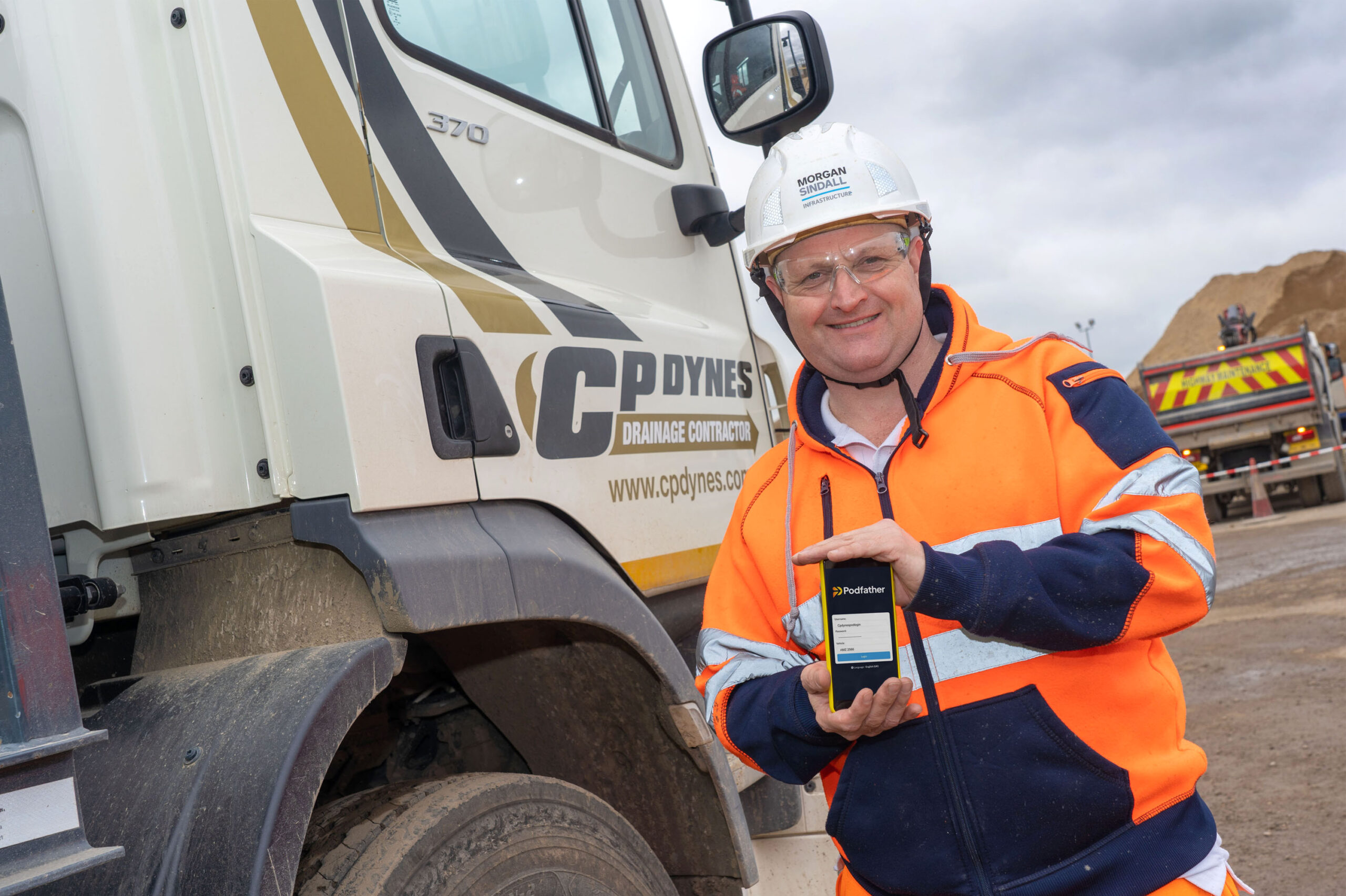
Management software might seem a million miles away from muck shifting but one groundworks specialist is reaping the rewards from its use. CPN hears how it’s doing it.
Groundwork and drainage specialist CP Dynes has implemented Podfather fleet logistics software to help manage the movement of hundreds of cubic tonnes of excavated waste a month. Working for Morgan Sindall on a £65 million upgrade of the A12, the contractor has increased productivity, improved visibility and streamlined its reporting using Podfather’s logistics planning, route optimisation and ePOD solution. The Essex-based firm has also improved safety, with automated vehicle checks, and reduced its environmental impact with a virtually paperless transport operation.
“The adoption of Podfather was part of a general upgrade of our management and reporting systems,” explains Rhys Dynes, a second generation member of the family run business. “We have been operating for more than thirty years during which time we have grown significantly from our first contract which was valued at £1.5k to drainage projects worth in excess of £10m.
“To support this growth, we are transitioning from old school working practices to more streamlined, digital processes that allow us to capture, record, store and access detailed operational information,” he continues. “This move to ‘e’ systems, of which Podfather is a fundamental part, also includes an upgrade of various back-office and accounting applications.”
The firm originally introduced Podfather to replace paper tickets used to record and report on the movement of muck from concrete replacement projects on the A12 in Essex. With on average 1,200 loads a month, totalling around 10,000m3, the contractor previously relied on drivers manually recording the type of material, number of loads, drop off points and hours worked. Completed tickets needed to be returned to the office where the information was collated for customer reporting, invoicing and payroll.
Using Podfather, it can now reactively plan its mobile operation. With real-time visibility of all vehicles, management can react to changes on-site or on the roads, and adjust the resource allocated accordingly. “For example, yesterday we did 30 loads to landfill and, due to light traffic and good running times, we were able to move a vehicle off that job and onto another project. Today is looking similar but tomorrow who knows?” adds contract manager Jack Hutchison. “Using Podfather we can react and adjust accordingly which means each vehicle is optimised in its use and we are overall more productive and efficient.”
Podfather’s automated ticketing features are also improving the utilisation of the company’s specialist fleet as drivers no longer have to fill in duplicate copies of paperwork to show what loads have been transported and where. Once the days’ schedule has been planned in Podfather, instructions are shared with the drivers’ mobile device using the app. This gives the driver the point of pick and drop off, and the route in between, it also allows them to record details of the load, using customised drop-down boxes, together with date, time, location stamped photos and signatures.
“Using Podfather we have the information we need, when we need it,” concludes Dynes. “We can answer customer or management queries at the click of a button, rather than taking hours sifting through paperwork, and we can even empower our clients giving them access to the system to self-serve information.
“This has had a positive impact for our drivers who spend less time filling in paperwork and more time driving, our back-office team who don’t have to spend hours transcribing paper tickets and for our customers who have a fully documented, evidentially supported audit trail. It’s also good for the environment and good for us as a business both in terms of growth and reputation.”