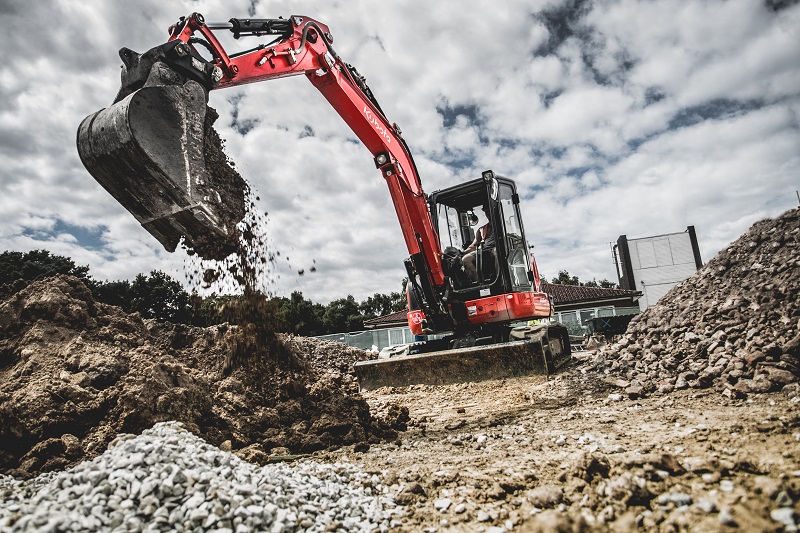
Construction Plant News spoke to Leana Horton, Key Account Manager at Kubota UK, on the the rise of telematics within the construction industry.
Telematics has been utilised within haulage, logistics and quarrying industries for quite some time, but within the last five years we have seen the technology become a real buzz word within the construction and plant sector.
More and more, we are seeing telematics solutions being fitted to the construction plant machinery being used on projects. The technology is already delivering considerable solutions and benefits to plant hire firms and contractors throughout the UK, however its full potential is yet to be delivered industry wide.
A brief history of telemetry
As a technology, telematics in its basic form has been around for decades, with GPS tracking on trucks and fleet vehicles within the logistics, haulage and quarrying industries enabling fleet managers to view the whereabouts and performance of a vehicle (such as tonnage per hour, to use a quarrying example).
However, as stricter EU emmisons legislation has imposed regulations on a wider array of vehicle types and sizes, engines have become more advanced and as a result are integrated with electrical management software that withdraws data from the engine, reporting on a number of metrics including engines emissions and service diagnostics.
Linked with these developments to meet legislative requirements, telematics has taken strides forwards with how it can communicate its data, enabling real time reports to be produced, stored and accessed.
What’s more, since the introduction of mobile devices, this data can be accessed from remote locations, whether on the job or from a central office.
Due to these significant advancements within telemetry and EU legislation pushing emissions regulations within more industries, telematics has become popular within quarrying, agriculture, forestry and is now it is gaining real traction within the construction and plant sector too.
Telematics solutions
There are a myriad of benefits and solutions that telematics can offer to the construction sector, for the plant fleet owner, hiring contractor and the operator alike.
These telemetry solutions can enable improved operational productivity, machine security, energy efficiency and service diagnostics to ensure guaranteed uptime – all leading to improved fleet management as a whole.
Telemetry ensures that fleet owners have site of whether their machines are being properly maintained when hired out, whilst also making sure the contractors are getting maximum value during the course of the hire period.
Theft prevention, security and tracking
On any building project, financial security and health and safety are of the utmost importance, with businesses often suffering substantial monetary losses through the theft and misuse of plant equipment, but also due to breach of health and safety laws.
Ensuring peace of mind for both the contractor and machinery owner, the up-to-the-minute telemetry data delivered can track a single machine or an entire fleet 24/7, alerting the fleet manager if the vehicle has been moved from site, with the option of the fleet manager to remotely immobilise the machinery if required, helping to maximise the prevention of theft.
For instance, if the machinery has been stolen during the night, telematics can locate the machine whether or not its power is switched on. In the case of instances of theft, vandalism and out of hours use, the fleet manager will be immediately alerted when the incident occurs.
Further to this, the sensors and telemetry unit review in real time the operational output of the machine and track its movements on site.
This is of great benefit, not only for the fleet manager, but also to the operator. Using mobile hardware such as a tablet within the cab, the operator will be alerted if they stray from their geo-fenced working area.
If the operator does not react to the audible alert, the site manager can resort to remote immobilisation, again ensuring utmost health and safety is maintained.
This technology is equally valuable to the fleet owner, as when hired out, they can track the movements and operational uptime of the machine.
This means that they will be alerted if the machine is used out of the Construction Planthire Association’s (CPA) weekly usage guidelines or the contactor’s contractual obligations. If this does take place, the additional charges required can be applied in full confidence due to the data reported.
Emissions, maintenance and operator monitoring
In addition to security and health and safety solutions, telematics can also be used to report on a machine’s emissions, maintenance, service demands and the performance of the operator using the machine.
If a machine is suddenly hemoraeging fuel or a component part is underperforming, the fleet manager will be alerted and the problem can then be rectified. If the issue is due to poor operating standard, this can be fed back and the right respective training can be implemented to resolve any operational issues.
On the other hand, if it is an issue with the machine itself, the diagnostics function can inform the fleet manager what the specific issue is and what needs servicing.
Not only is this valuable in conserving fuel and maintaining the highest possible productivity for the machine’s usage on site, but it enables the equipment owner to carry out these checks before hiring out the machinery to make sure each piece of kit is in full working order before going out the door. The environmental benefit is sizeable too, reducing a project’s carbon footprint.
The age of construction machinery telematics is here. Telemetry can ensure greater machine security, on site health and safety, emissions control, operational uptime, fleet management and reduce a project’s carbon footprint.
Make sure you reap the benefits on offer by ensuring every piece of plant machinery purchased or hired is fitted with a plant telemetry solution.
For more information on Kubota and its telematics partnership with Trakm8, click here.