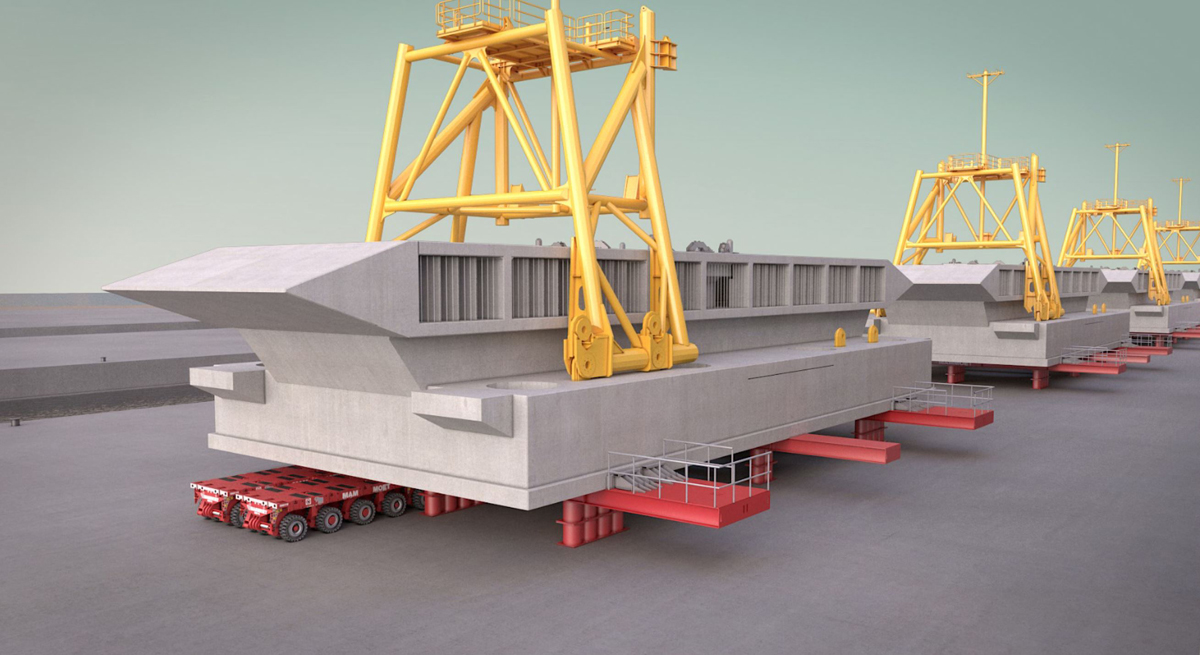
Topcon helps streamline nuclear power plant construction project
In the UK we currently generate around 15 to 20 per cent of our electricity from nuclear energy. To support the UK Government commitment to reach Net Zero emissions by 2050, Hinkley Point C in Somerset is under construction. This is the first new nuclear power station to be built in the UK in over 20 years and will provide low-carbon electricity for around 6 million homes. The electricity generated by its two EPR reactors will offset 9 million tonnes of carbon dioxide emissions a year, or 600 million tonnes over its 60-year lifespan.
As part of the project, Balfour Beatty is responsible for delivering the complex marine and tunnelling works, and constructing the structures for the critical infrastructure needed to supply cooling water to the power station. This project involves the construction of three tunnels under the Bristol Channel, with offshore concrete heads allowing sea water to pass into the tunnels.
Building on its well-established partnership with Topcon, Balfour Beatty used the Topcon ClearEdge3D Verity software system to ensure that a key part of the project was completed accurately, on time and on budget.
Working within tight tolerances
Through the delivery stages from design to offshore execution, precision was vital with very tight construction tolerances required. Once complete, the system will be connected to the seabed via vertical shafts, capped with intake and outfall heads. The intake structures are 44 metres long, which is roughly the length of four double-decker buses, and around eight metres high, weighing more than 5,000 tonnes each.
The structures were constructed at a purpose-built facility at Balfour Beatty’s site in Avonmouth, Bristol. Large steel alignment frames were then installed on top of the heads to enable future lifting and piling operations.
Lifting lugs were cast into the reinforced concrete heads and these were then matched against bespoke handling frames. The accuracy of the fit was critical due to the 5mm tolerance available for alignment, ultimately allowing for the installation of the lifting pins and the subsequent safe offshore lifts.
Tom Bush, Digital Project Delivery Coordinator at Balfour Beatty, explained: “It’s no surprise that using cranes to rotate and position the large fabricated structures on to the concrete heads is an incredibly challenging task, and we didn’t have any room for error. While we were constructing the concrete heads, fabricators were building the alignment frames. With such a small tolerance on either side of the lifting lugs, we needed to ensure the data and measurements we were giving were accurate – with Topcon’s ClearEdge3D Verity software, we were able to do that.”
Verification of works
The team used Topcon’s ClearEdge3D Verity software, which rapidly compares point cloud data with design and fabrication models for verification of work. Balfour Beatty used the software to compare real-time data being supplied by the survey team on-site against initial drawings, to ensure the lifting lugs were aligned with the tolerance available. Inaccuracies were discovered during the first comparisons, and so changes were fed back to the fabricators and rectified early on.
Topcon’s software was also used to run several scenarios and create a digitally accurate approach that saved Balfour Beatty time and money, as well as strengthening health and safety precautions. The software translated data collected on-site into a digital model, providing accurate demonstrations of the rotations and twists of the installed lifting lugs on each of the heads, with immediate access to the latest data and comprehensive digital display models helping to streamline the process.
Tom Bush continued: “Being able accurately verify the position of each individual lifting lug on each of the concrete heads through Verity allowed us to provide detailed as-built information, within a short period of time and remove the risk of expensive or time-consuming errors taking place when it came to fabricating and fitting the alignment frames. This was key to enable the project to keep on programme.
Adam Box, Business Development Manager for Vertical Construction at Topcon Positioning Europe, said: “Balfour Beatty had quite the task at hand with this project but, thanks to the Verity software, they’ve been able to verify the work carried out at every stage of the process and ensure a success when it came to installing the frames to the heads. We worked closely with the Balfour Beatty team to ensure the software was being used to its full potential, to help reduce the risks of timely and costly errors taking place, and to deliver the project on time.”
For more information about Topcon’s ClearEdge3D Verity software system and range of digital technologies, visit: https://www.topconpositioning.com/gb/office-software-and-services/uav-and-scanning-software/clearedge3d-verity.