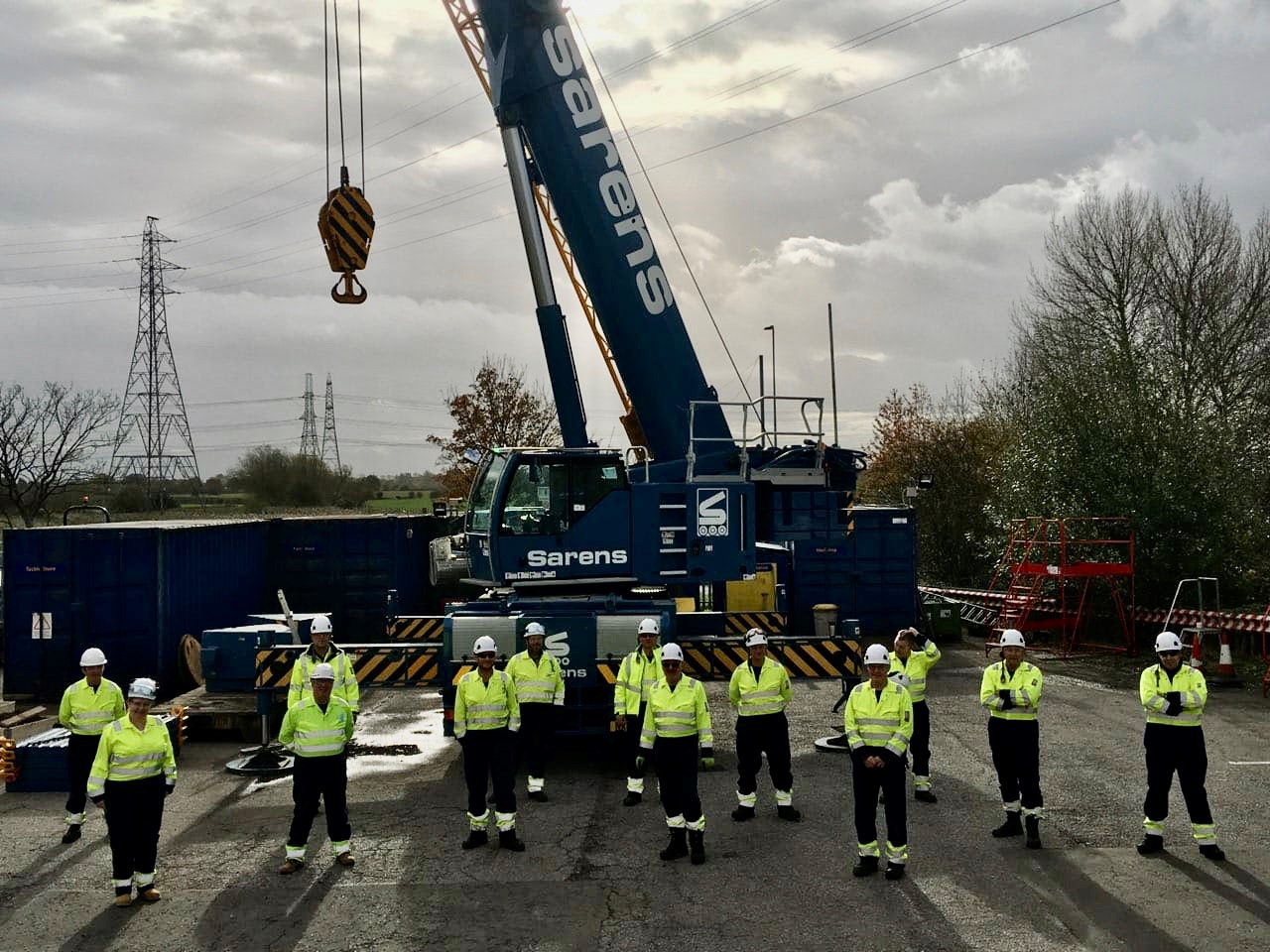
Sarens, the heavy lifting, engineered transport and crane rental specialist, has been directly involved in the turnaround, upgrade and improvement works that have taken place at the Essar Stanlow refinery.
The works – carrying out major maintenance and repair operations throughout the facility – have affected critical plant infrastructure such as the cracking unit and have been spread over more than nine weeks.
For the project, Sarens deployed 39 cranes of various sizes, with load capacities ranging from 12 to 750 tonnes, as well as 55 members of its engineering team and technical staff to the Essar site, 16 of whom have been permanent staff at the Sarens depot at the refinery since November 2020. In addition, during the operation, the team also used different units of SPMTs (self-propelled modular trailers) and other jacking and skidding systems to transport materials inside the plant.
To facilitate manoeuvering and optimise transport processes, its technical team used, among other resources, a programmable electronic steering system for its SPMTs, with the aim of providing accurate alignment of plant during the installation. In addition, new structural steel supports designed and provided by Sarens for the LR1750 crane – the one with the highest load capacity used on this occasion – were also used as a pedestal to pick-up a set of existing ring piles, to avoid the need for site civil works.
Essar’s Stanlow plant is one of the largest in terms of production volume in the UK. It is currently responsible for the production of up to 16% of the fuels used by British transport, especially in the NorthWest region. The plant produces 4.4bn litres of diesel, 3bn litres of petrol per year – enough for a vehicle to drive around the world 20 million times – and up to 2bn litres of jet fuel per year.
This project, the first of this magnitude since spring 2018, has required the shutdown of virtually all the refinery’s units to comply with the inspections required by regulators, as well as to carry out various overhauls and upgrades to essential equipment and the installation of new equipment, necessary to maintain the plant’s operation continuously and without downtimes.