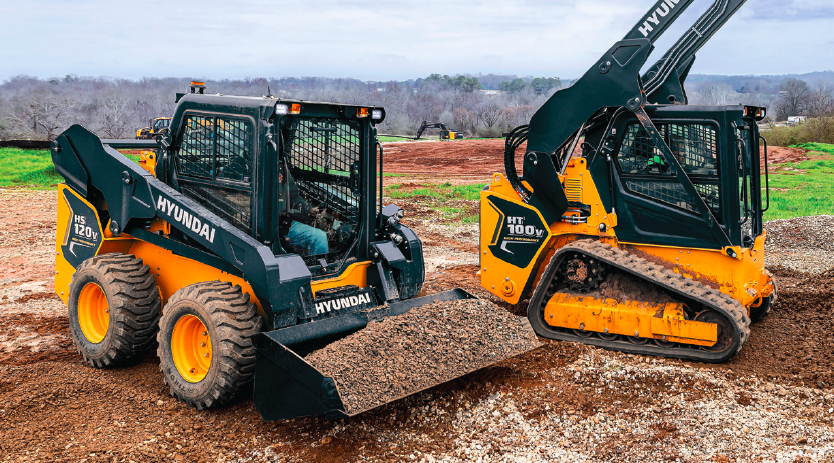
They might be small in stature, but today’s compact machines are packing a bigger and bigger punch, making them a valuable addition to any fleet. CPN rounds up a few of the latest models that are making a splash.
Whether it was the influence of Bauma or not, there seems to have been a flurry of new launches and updates in the compact equipment market. Probably for good reason. These small machines play a vital and expanding role on sites, enabled by a huge increase in their capabilities despite their mini dimensions. Basically, you get a lot of machine for your money.
One of the major names to up the ante is Hyundai Construction Equipment. It recently launched two skid steer loaders (SSL) and a compact tracked loader (CTL). Versatile and highly productive, these compact models are being targeted to take the company into new market sectors and provide additional options for existing customers.
The HS80V and HS120V skid steer loaders, along with the HT100V compact tracked loader, are powered by Hyundai Stage V diesel engines, delivering 49.5kW (66.4hp) in the smaller skid steer and 54.9kW (73.6hp) in the larger model and in the tracked machine. The engines meet EU Stage V emissions standards without the need for a diesel exhaust fluid after-treatment system.
The 3.2-tonne HS80V has a rated operating capacity at 50% tipping load of 885kg, while the larger 3.7-tonne HS120V delivers a maximum at 50% tipping load of 1,220kg. The tracked machine, which tips the scales at 4.4 tonnes, has a rated operating capacity at 50% tipping load of 1,490kg.
All three of the compact machines come equipped with vertical lift path loader arm geometry, which allows the boom to raise the bucket to full height without spilling material. The vertical lift path delivers improved stability, increased lift height and a higher operating capacity, boosting productivity. An auto self-levelling system ensures that the bucket or forks remain level throughout the lift arc, without the need for operator input.
The HS80V has single speed travel motors, offering a maximum of 11.9km/h. The larger HS120V comes with two-speed travel motors, with a top speed of 19.8km/h. The tracked HT100V also comes with twin-speed travel, offering a maximum of 11.5km/h. The two larger machines also offer optional highflow hydraulics, with the skid steer delivering up to 128.8 litres/min of flow and the CTL offering a maximum of 82.9 litres/min. The compact models are equipped with an industry-standard flat-faced hydraulic quick coupler, allowing operators to change attachments at the touch of a button from within the cab. A 14-pin electrical connector is also available, to control various attachments.
The machines are controlled through two multi-function joysticks, with multiple thumb and finger switches for auxiliary hydraulics and other functions. The righthand lever operates the boom and bucket functions, with buttons for auxiliary hydraulic flow and an electrical supply. The left-hand lever controls all driving functions, with a button for two-speed driving where supplied. Engine speed can be controlled by a rotary dial on the control panel, or by a foot pedal. The rotary dial is particularly suitable for constant speed operation, such as when working with powered attachments like a planer or a sweeper.
All three are offered with a ride control system, which uses a hydraulic accumulator to allow the loader arms to float slightly during travel. This minimises shock loadings to the operator cab and ensures material stays in the bucket.
The skid steers and compact tracked loader can be specified with Hyundai’s Hi MATE telematic monitoring system. With access through the Hi MATE app or online, the system provides customers with realtime machine performance data, location and access to diagnostics. Service and maintenance can be planned more effectively, guaranteeing increased uptime on site.
Making a dash
Eager to build on the success of its dash 5 mini excavator range Komatsu updated the line-up to incorporate several new features designed to improve safety, operator comfort, and versatility, while staying true to the core values that have made the dash 5 range a trusted choice for professionals worldwide.
The company says it arrived at the upgrades after listening to customers and focused its efforts on enhancing the features that matter such as safety, durability and ease of use. This new range is said to deliver on all fronts, providing operators with the tools they need to tackle any job with confidence.
Key improvements to the new mini excavator range include a rear-view camera, that is now standard from the PC24MR-5 and up. It offers a clear image with high resolution and wide viewing angle for comprehensive rear visibility. A dedicated monitor provides a wide unobstructed display, separate from the main vehicle screen.
For improved operator comfort a new air suspension seat comes as standard starting at the PC33MR-5. It is fully adjustable to ensure personalised comfort and ergonomics. And while in the cab operators will be able to get a better sight of what they are doing thanks to new LED lights across the whole mini HE range. These powerful, energy-efficient units provide bright, uniform illumination for enhanced visibility in low-light conditions. The lens design minimises glare and light scatter, reducing eye strain and improving safety.
Tools of the trade
Not to be outdone Takeuchi has launched a new 7.5 tonne wheeled excavator, the TB370W. The manufacturer claims it is a powerful compact machine that doubles as a versatile tool carrier designed for maximum productivity on busy construction sites.
Its offset 2-piece boom delivers an increased working range and added in-field lifting capacity, complete with lift overload alarm and arm, swing and boom holding check valves, all as standard.
The powerful and responsive load sensing hydraulic system supplies up to four auxiliary ports with hi-flow and proportional control, with optional multifunction grip allowing the operator to assign buttons to frequently used functions. It offers three different work modes Std, Eco and Eco Plus; Eco Plus switches between std and eco dependent on load. Operators can also switch to cruise control for consistent travel speed while simultaneously operating attachments.
As a multi-tool-carrier, the new TB370W with DPF, 4WD and 4-speed transmission delivers fast powerful productivity. The heavy-duty undercarriage with mudguards, switchable difflock and intelligent auto digging brake are said to deliver excellent safety and stability on site. The TB370W is available with optional outriggers. The large comfortable cab puts the operator in control with touchscreen and jog dial technology for every function complete with maximum safety and visibility with three auto cameras and full LED lighting all-round.
Its tilt-up cab provides good ground level access to all service and component parts. The TB370W is supported by a 5-year telematics subscription to Takeuchi Fleet Management (TFM) and now features a 3-year/ 3000- hour full warranty across the range.
Generation gain
Caterpillar has also weighed in with the introduction of eight new next generation skid steer loader (SSL) and compact track loader (CTL) models. Four new Cat SSLs – the Cat 250, 260, 270, and 270 XE – herald the next generation design to the SSL line. Meanwhile, the new Cat 275, 275 XE, 285 and 285 XE mark the expansion of the next generation design for the CTL line, joining the 255 and 265 announced in late 2023 (see The Dig this month). The largest CTLs ever produced by Caterpillar, the new Cat 285 and 285 XE compete in a new class size with greater lift height and lift and tilt breakout forces.
Maintaining the DNA of what made the Cat D3 series a leader, the next generation SSL and CTL models are a ground-up redesign that improves on the features that made the previous series popular. High performance is the standard for these next generation machines, with upgrades in engine power and torque, lift and tilt breakout forces, stability, operator comfort, and technology. The new SSL and CTL models carry on Caterpillar’s new machine nomenclature with the elimination of the series letter designation. All next generation Cat SSLs are now identified by an ending model number of 0, while all CTLs have a model number ending in 5. Simplifying nomenclature, the middle number represents machine size with a larger number designating a larger machine.
All next generation Cat SSL and CTL models feature a redesigned engine compartment that places the engine and cooling package lower into the frame for improved stability, giving the operator confidence in handling heavy loads throughout all aspects of the work cycles.
Meeting U.S. EPA Tier 4 Final/EU Stage V emissions standards, the four new CTL models are powered by the Cat C3.6TA engine, while the 250 and 260 SSLs are powered by the Cat C2.8T and the 270 and 270 XE by the Cat 3.6TA. These new engines maintain horsepower across a wider rpm range compared to the previous engines powering the D3 series and boast significant torque increases – 13% for the 250 and 260, 35% for the 270, and 50% for the 275 and 285 – for improved working performance. With a vertical lift design, these new next generation machines feature significant increases in lift height, breakout forces and ROC to elevate loader flexibility and performance.
Their new closed-centre auxiliary hydraulic system allows these machines to operate all Cat smart attachments with the standard hydraulics provided. Standard hydraulic system pressure increases 5% to 3,500 psi (24130 kPa) in the next generation models. Cat 250, 260, 270 and 275 machines equipped with standard hydraulic flow are shipped from the factory outfitted as “High Flow ready.” High Flow functionality is activated simply via a new software enabled attachment (SEA), permitting on-machine or remote activation of increased hydraulic flow to 30 gal/min (113 l/min) for the 250, 260, and 270 models and 34 gal/min (129 l/min) for the 275 at standard hydraulic system pressure.
Also available, the High Flow XPS factory option increases auxiliary hydraulic system pressure to 4,061 psi (28000 kPa) for the 250, 260, 270, 275 and 285 next generation models. Along with this, hydraulic flow is increased to 30 gal/min (113 l/min) on the 250, while flow increases to 34 gal/min (129 l/min) for the 260, 270, 275 and 285 models. Equipping the 250 with the High Flow XPS option gives customers auxiliary hydraulic performance not available before in a mid-size chassis SSL. Equipped for maximum hydraulic capability, the High Flow option for 270 XE, 275 XE and 285 XE loaders increases auxiliary hydraulic system pressure to 4,496 psi (31000 kPa) and hydraulic flow to 40 gal/min (150 l/min).
The four next generation CTL models feature a new E-bar (equalizer bar) undercarriage that provides increased stability for grading and handling heavier loads. The E-bar undercarriage delivers the benefits of a rigid-style undercarriage design when lifting heavy loads or using heavy attachments like mulchers and dozer and grader blades, while simultaneously providing the benefits of an oscillating undercarriage when encountering uneven terrain or obstacles.
All next generation Cat SSLs and CTLs feature a larger cab design with 22% more overall volume and 26% additional foot space. With a 2.75-in (70-mm) increase in interior width, the new cab expands footwell-to-ceiling height by 1.8 in (46 mm) and allows for an additional 1.5 in (40 mm) of hip room and 1.1 in (28 mm) more width between the joysticks to improve operator comfort.
Next generation loaders are equipped with either a 5-in (127-mm) standard LCD monitor or an 8-in (203-mm) advanced touchscreen monitor, depending on the selected technology package. Like the advanced display on the D3 series, the standard monitor features Bluetooth connectivity and supports functionality for rearview camera feed, creep, job clock, maintenance reminders and 32 languages. The new advanced joysticks enable integrated control of the advanced touchscreen monitor, so all machine function control and adjustments can be made without the operator removing their hands from the controls.
Caterpillar believes that these new SSLs and CTLs offer the next level of integration between machine and technology. Both standard and advanced monitors provide the ability to run Cat smart attachments, such as the dozer and grader blades and backhoe. Attachment operation is integrated into the joysticks, and the machine automatically recognises the type of attachment and the required joystick pattern for controlling it.
Available Cat Product Link Elite tracks machine hours, location, and asset utilisation, provides fault code details, and delivers advanced monitoring and machine health with data remotely accessible via VisionLink. Additionally, Product Link Elite provides remote flash and remote troubleshooting capabilities and quickly enables the remote activation of the SEA High Flow feature.
Electric dreams
Kubota first introduced its prototype 2.5 tonne electric excavator at Intermat in 2012, marking the beginning of its journey into electrification. Now, the company is taking another significant step forward by unveiling an electric retrofit option for the KX019 (1.8-tonne) and U27-4 (2.5-tonne) diggers. The whole idea is to make the transition to electric equipment more accessible and practical for owner/operators. With global demand for sustainable alternatives on the rise, Kubota says it is addressing key industry needs, namely reusability and longevity of machinery. This new solution enables customers to replace the standard diesel engine of their excavator with a modular battery pack. Alternatively, machines can be fitted with the battery pack from new and later swapped out for a diesel engine or vice versa.
Cost has always been a barrier to adopting electric machinery. But with this retrofit solution, customers gain flexibility. They can enjoy the low running costs of electric and still have the option to switch to diesel if necessary. It’s about providing choice and easing the transition to a greener future. Kubota’s solution also notably reduces maintenance costs and operational overheads. With no engine and associated components, servicing time and expenses are considerably reduced, saving customers both time and money. Additionally, with electricity costing far less than fossil fuels, it offers a highly economical advantage.
But this isn’t all, the retrofit solution delivers low noise levels, making it ideal for urban environments and indoor applications. Noise levels at the operator station are significantly lower compared to the diesel equivalent, enabling better communication and safety with co-workers.
Quiet operation also allows for longer working days, maximising time on-site and accelerating project timelines. Kubota’s solution addresses the unique needs of construction operators, recognising that many machines only operate for a few hours a day, often less than two hours. The battery pack’s runtime aligns with this usage, and with the ability to top up charges throughout the day, working hours can be easily extended.
While electric models are yet to dominate the market, Kubota’s approach is focused and practical, aimed at providing an easier path to adopting electric technology without abandoning the flexibility of existing diesel setups. By offering a solution that bridges the gap between traditional and electric machinery, Kubota is looking to make significant strides towards a more sustainable industry. The electric retrofit is expected to roll out throughout 2025.
For more on Hyundai: WWW.RDR.LINK/CBB014
For more on Komatsu: WWW.RDR.LINK/CBB015
For more on Takeuchi: WWW.RDR.LINK/CBB016
For more on Caterpillar: WWW.RDR.LINK/CBB017
For more on Kubota: WWW.RDR.LINK/CBB018