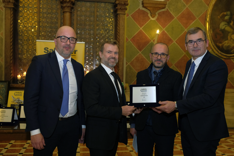
The first fully electric, battery-powered mini-excavator from Wacker Neuson, EZ17e, performs and handles just like a diesel-powered model. For this innovative development, the jury of the SaMoTer Innovation Award 2020 awarded the electric mini-excavator with the Innovation Award in the category hydraulic mini-excavators.
Wacker Neuson is strengthening its position as an innovation leader in the zero emission segment with machines like the fully electric excavator EZ17e. In Verona, the mini-excavator was awarded with the SaMoTer Innovation Award 2020. The innovation was selected in the category hydraulic mini-excavators, among other things, for its efficiency, the optimal integration of the electric drive as well as its performance, which corresponds to that of the diesel-powered model. The excavator will be the highlight product at the Wacker Neuson stand C11-C12 at SaMoTer in Verona, that is taking place from March 21-25, 2020. “We are looking forward to presenting our broad offer of zero emission products to the trade fair visitors, including the electric mini-excavator EZ17e, which the trade fair awarded with the SaMoTer Innovation Award,” says Georg Jung, Managing Director of Wacker Neuson Italy. “Already today an entire inner city construction site can be operated with Wacker Neuson emission-free solutions.”
High flexibility in use
The excavator EZ17e can run entirely on its battery. Yet, it can also be operated while connected to the mains – and even charged while in operation – thanks to its smart charging management system. This makes it the ideal solution for environments where emissions and noise have to be kept to a minimum, for example in urban areas, for indoor work or on sites close to schools and hospitals. Combined with other solutions in the Wacker Neuson zero emission range, this machine can contribute to reducing noise and eliminating emissions on construction sites. As the mini-excavator is a zero tail model, it offers no overhang. Operators do not have to worry about damaging the machine when working close to walls or in confined spaces as the tail of the excavator never extends beyond the undercarriage. This also makes the EZ17e ideal for tunnel construction, demolition and redevelopment work in confined spaces, as well as for restoration projects inside buildings. These are precisely the types of environments where contractors need powerful, compact machines that can be operated without any emissions.
No compromises in performance
“Wacker Neuson has been manufacturing innovative, practical and cost-efficient equipment for 170 years. We’ve channeled years of experience and expertise in zero emission products into our first mini-excavator with battery and electric drive technology. Our development work always focuses on usability and customer value. Which is why we make no compromises when it comes to performance, with power ratings matching those of our diesel-powered model,” explains Martin Lehner, CEO of the Wacker Neuson Group. All hydraulic functions are as powerful as those of the conventional model. The battery is integrated in the existing engine compartment. The EZ17e weighs almost exactly the same as the diesel version and can therefore be transported on a trailer.
Easy to handle – low maintenance – reliable drive
The electric excavator EZ17e is powered by the latest lithium-ion technology, which Wacker Neuson has been using and continuously developing for many years now. Long battery life is one of the key features here, allowing the fully electric excavator to be operated for a full working day. The battery can be charged overnight via a domestic socket (110-230 V), or in just four hours using a high-voltage current. Service teams do not need any extra training for servicing the machine, making the electric excavator particularly attractive to rental parks. “Electric drives are becoming increasingly important. For rental companies in particular, these solutions are an interesting supplement to existing fleets as many of their customers rent products for specific projects such as renovation work inside buildings or tunnel construction,” adds Alexander Greschner, CSO of the Wacker Neuson Group. “Electric drives are also low maintenance. This is a huge benefit as it reduces maintenance time and costs and maximizes machine availability.”