The Building Safety Group (BSG) has reported a 40% increase in PUWER equipment breaches occurring on construction sites during the first half of 2021. BSG’s latest figures were obtained following 8,500 independent site inspections that were conducted between 1st January and 30th June. The 40% increase was identified when comparing Q1 with Q2 figures.
PUWER stands for the Provision and Use of Work Equipment Regulations (1998). It places duties on people and companies who own, operate, or have control over work equipment. PUWER regulations are enforced by HSE inspectors during regular checks. An improvement notice will be placed on a piece of equipment if a health and safety inspector feels that it has not been subject to inspections and risk assessments detailed under PUWER. In these instances, the inspector will tell the business owner what actions they need to take to comply with PUWER regulations and give them a period of 21 days to put these actions into place. If the actions are not followed within this period a prohibition notice will be enforced, preventing the owner from using the equipment.
BSG’s inspection report comes at a time when the HSE is increasing its focus on enforcing PUWER regulations, following concerns that the condition of some machines may have degraded because of long periods of inactivity due to COVID-19. This can lead to equipment corrosion and possible seizure, putting workers at greater risk.
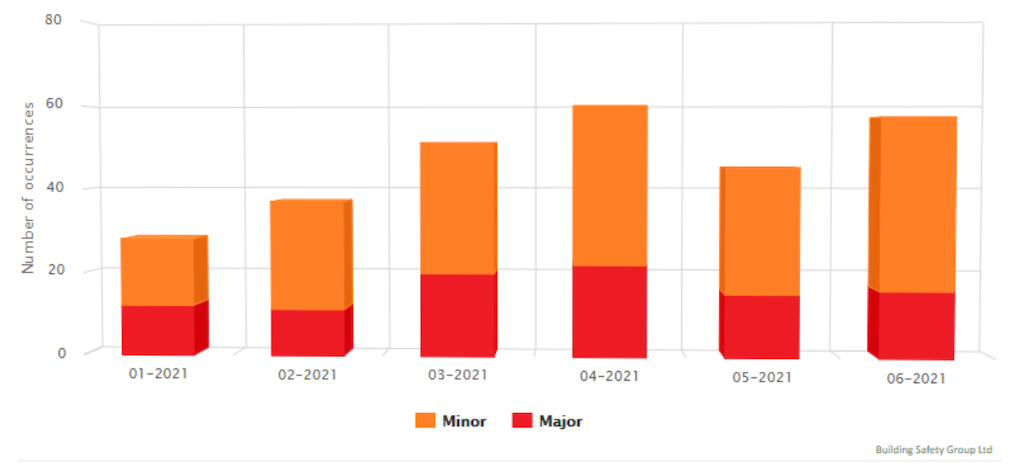
The consequences of not adhering to PUWER regulations were made tragically clear in 2017 when a construction equipment-hire company was prosecuted, following the death of an employee. AGD Equipment Ltd, based in Warwickshire, received an £800,000 fine after a worker was killed. The case, which was brought before Warwick Crown Court, revealed how Mark Seward was testing a hydraulic cylinder when the cylinder cracked under pressure, exploding, and sending metal fragments flying. One of these hit the employee in the head. The Health and Safety Executive’s (HSE) investigation found that AGD Equipment had not told Seward the safe working pressure for the cylinder. The task was not adequately supervised, and the company had not erected protective screens to stop staff being injured by projectiles.
AGD pleaded guilty to breaching regs 12(1) of the Provision and Use of Work Equipment Regulations (PUWER 1998) and 3(1) of the Management of Health and Safety at Work Regulations (1999), for failing to risk assess the task. AGD Equipment was fined £800,000 and ordered to pay costs of £28,711.
Andy Harper, Technical Support Manager at BSG commented: “Businesses need to look at PUWER regulations closely and make note of what is considered ‘work equipment’ which is a ‘catch all’ term that covers any tool, appliance, or piece of machinery that could potentially pose a risk to employees.” Andy added: “PUWER regulations require a competent person to periodically inspect each piece of work equipment to ensure it is fit for use, and to officially record their findings for future reference. With more complex pieces of machinery, instructions on how to use the equipment, alongside any potential safety issues, should be made available to all equipment users.”
For further information about PUWER and how these regulations apply to your business,
please contact us: buildingsafetygroup@bsgltd.co.uk