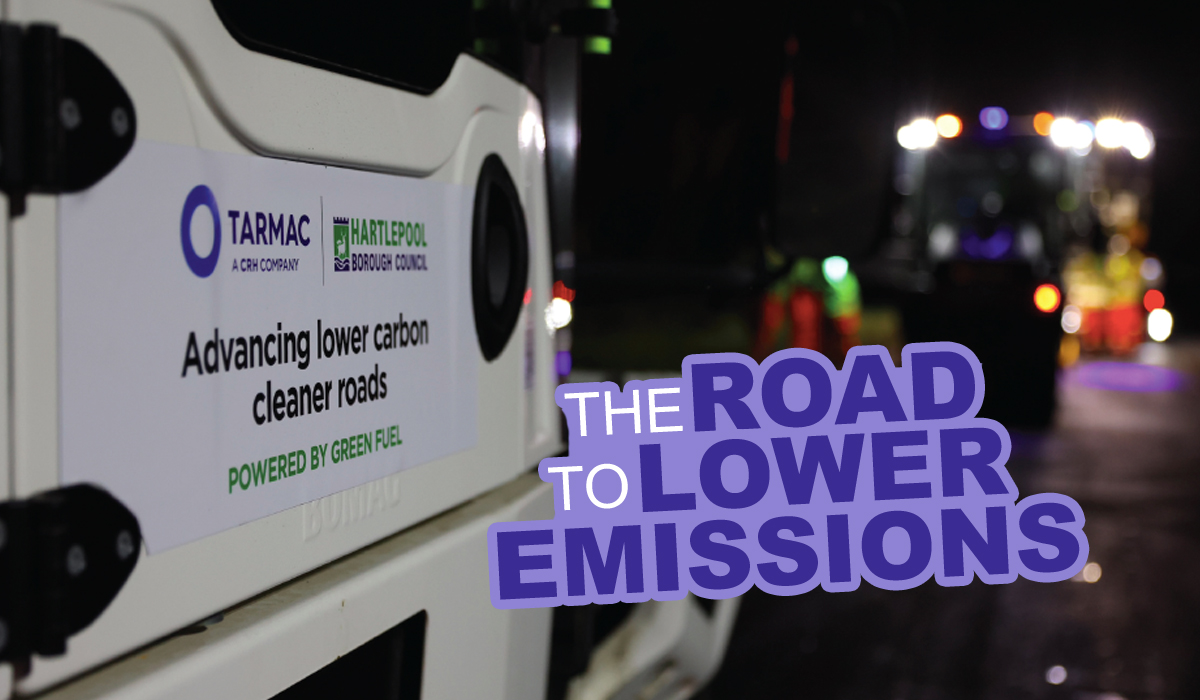
A small resurfacing project in northeast England could point the way to decarbonising road maintenance. CPN reports.
Three local roads in the North East have become the lowest carbon highways ever to be resurfaced in the UK, thanks to a project that has set a new benchmark for the way roads are maintained. The participants, which included local councils, equipment manufacturers and contractors, reckon to have cut the carbon emissions of these road schemes by up to 80% compared to projects using traditional methods.
One of the main companies behind the initiative, Tarmac, says that the schemes achieved the lowest CO emissions for road resurfacing in the UK without using carbon offsetting.
Tarmac said the project arose after holding a series of joint workshops in the North East of England with Shell Bitumen “ looking at sustainable road solutions and the art of the possible”, when two councils, Stockton-on-Tees Borough Council and Hartlepool Borough Council, said that they had road projects comingup that might be suitable to test out low carbon working methods for resurfacing roads.
Working together with international partners such as Shell, Volvo CE, Wirtgen and JCB, the team set out to devise a low carbon strategy to resurface a section of the A689 in Wynyard, near Hartlepool, and two residential roads in Stockton-on-Tees Borough: a total of 1.1 miles. Cutting carbon emissions where possible dictated everything, from the materials to be used to the plant operating on site.
“Our strategic partners for this project and other vehicle manufacturers are constantly innovating. We aimed to ensure we had as many electric vehicles as we could working on this project. However, there are some types of construction vehicles that are not yet available (or widely available) with electric engines.
Where this was not possible, we aimed to ensure that we could power vehicles with hydrotreated vegetable oil (HVO) instead,” said Brian Kent, technical director at Tarmac.
Volvo and Wirtgen, for instance, supplied a number of electric plant vehicles and prototypes including electric and hybrid road rollers and an electric bond coat sprayer. Greener Power Solutions supplied a battery unit for charging the electric vehicles on site as there was static charging infrastructure.
RAP delight
On the materials side, warm mix asphalt was used together with a newly-developed biocomponent binder from Shell that uses biogenic materials to create a technical carbon sink in the road that then stops carbon from being released into the atmosphere.
The surface course and lower layer of the pavements used 30 % recycled asphalt planings (RAP) in the lower layer and 20% in the surface course to reduce the need for primary materials. The asphalt was sourced from Tarmac’s manufacturing plant at Coxhoe, which kept carbon emissions to a minimum because the plant is powered by a combination of bio-fuel and electricity. The RAP was stored at the plant in
ZappShelters, so it could be stored in the same low moisture condition as it was received, meaning that the material did not require as much energy to dry it out before being mixed and so accelerating the manufacturing process, saving further fuel and carbon.
According to Tarmac, it routinely monitors the carbon emissions of all types of work it carries out, basing this on robust calculationssubject to the materials used, the power used at the plant and on the roadside and the carbon generated as part of the logistics process. “There is no one typical job and so we cannot provide an average road. However, our calculations show that this project has reduced carbon by 80% compared how we would normally have approached it using conventional materials and methods,” said Kent.
“A traditional road resurfacing project would use vehicles and plant running on diesel, hot mix asphalt and might not include a proportion of recycled material. For this project, we used a combination of new technology, including a new higher bio binder which has not been used anywhere in the UK to date, as well as high proportions of recycled asphalt planings (RAP) and had plant and vehicles running on HVO and electricity.”
Drilling down into the data revealed that the largest contributor to the significant carbon reductions on this project was manufacturing and transporting materials. This means that planning the logistics for any scheme is as crucial for cutting carbon emissions as it is for “This project is nationally significant because it provides a blueprint for how to decarbonise every element of highways delivery,” Kent concludes. “Our team has shown that it’s possible to significantly turn the decarbonisation dial with new material technologies, cutting-edge plant and collaborative working with local authorities and the supply chain.”
The full fleet consisted of:
■ Wirtgen EV 120 roller
■ Wirtgen HD90 hybrid roller
■ Volvo EV bond coat tanker
■ Volvo EV tractor unit (i.e. the power unit for an articulated truck)
■ Volvo EV tractor unit
■ Volvo loading shovels
More information on Tarmac