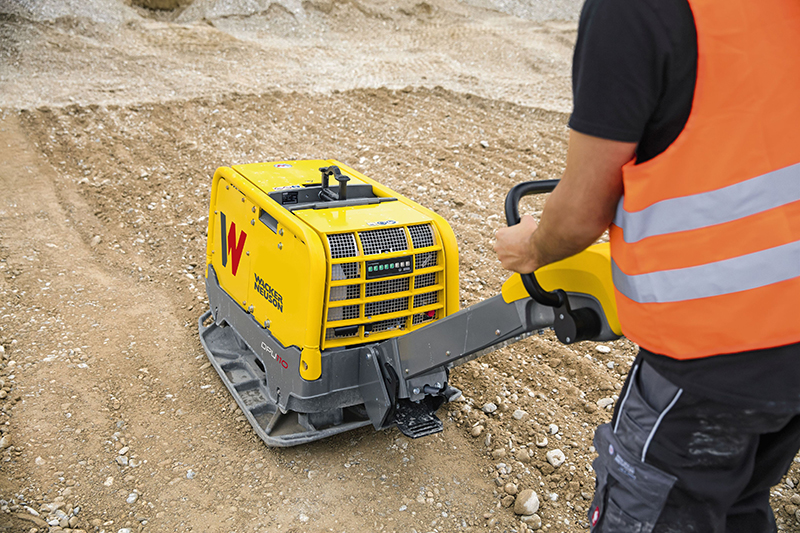
Wacker Neuson introduces Compamatic for heavy duty vibratory plates.
With the Compamatic solution, Wacker Neuson connects its compaction control with a Telematics solution. Compamatic is now also available for the heavy-duty reversible and some of the heavy-duty remote-controlled vibratory plates. This makes compaction progress traceable and allows for completely documented quality control. Customers can even more efficiently design the job site process using Compamatic.
Where has compaction been carried out already? How high is the degree of compaction? These typical project manager questions can be answered quickly and easily using Compamatic. Responsible persons can review from their desk whether all the work steps planned for the workday have been carried out, the planned surfaces compacted, and the degree of compaction everywhere is sufficient. This allows the next steps, such as planning the asphalt delivery, to be initiated quickly, efficiently and easily – without the project manager having to travel to the often remote construction sites for quality control.
Time and cost savings
Compamatic is a combination of the time-tested and proven Compatec compaction control by Wacker Neuson and a Telematics module. Wacker Neuson now also introduces the system for the reversible vibratory plates DPU80, DPU90, DPU110 and the remote-controlled versions DPU80r and DPU110r in the range from 80 to 110 Kilonewtons. Compamatic is likewise available for the coupling set of the DPU110 model. On the one hand, Compamatic results in enormous time savings on complex large construction sites, as quality assurance is enabled via the EquipCare Manager, therefore making fewer on-site inspections necessary. Even for small businesses, easier quality control results in time and cost savings. “Compamatic makes it easier for our customers to monitor and document soil compaction,” explains Stefan Pfetsch, Director of Sales at the Wacker Neuson production company in Reichertshofen. “The function is linked to our existing Telematics system EquipCare. Thus, all information is clearly displayed on one platform and easy to find.”
Traceable compaction progress
A vibratory plate equipped with Compamatic sends data for quality control to the Wacker Neuson EquipCare Telematics solution. The exact machine location is recorded via GPS. At the same time, the Compatec compaction control reads out the compaction data at the relevant point in time. In the EquipCare Manager, a satellite image with a “heat map” uses different colors to show where compaction has taken place and how much.
Easy and exact quality control
As Compamatic is integrated into Wacker Neuson’s existing EquipCare Telematics solution, customers can easily access machine data and check compaction progress via EquipCare Manager on a PC. The documentation and visualization of compaction provide a quick overview of work progress and compaction quality, as this no longer depends solely on the experience and assessment of the operator. In addition, the vibratory plates with the Compamatic module – like all compact machines equipped with EquipCare – are automatically located and visible in the portal for the user.
Since 2019, Wacker Neuson has been equipping compact equipment such as excavators, dumpers and wheel loaders with the EquipCare Telematics solution. This increases transparency in fleet management, as the machines send a report in real time to the customer’s terminal device when maintenance is required, or in the event of operational faults or unexpected relocations.