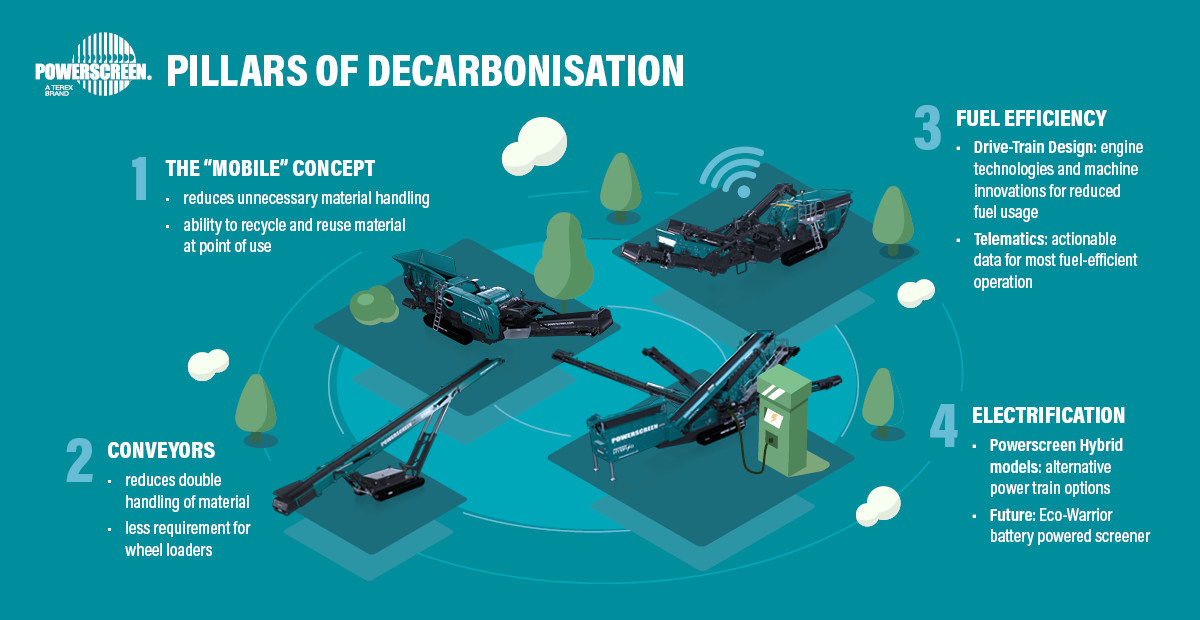
Powerscreen is responding to the industry’s decarbonisation challenge by providing solutions that work towards minimised environmental impact and greater sustainability.
Powerscreen’s decarbonisation story begins with the introduction of the concept of mobile crushing and screening, has evolved to increase fuel efficiency and looks to the future with Powerscreen’s electrification strategy, including an exciting, brand-new concept for the future of crushing and screening—the Eco-Warrior battery powered screener.
Neil Robinson, Powerscreen Product and Applications Manager says, “Some may view this topic as a recent trend, but for Powerscreen, decarbonisation is multi-faceted and has always been at our core. The Powerscreen mobile concept has always contributed towards decreasing the carbon footprint per tonne of material produced. This is done by reducing unnecessary material handling of hauling and loading material to static plants in aggregate production or in the ability to recycle and reuse material at point of use, for example in roadbuilding projects where sub-base material is produced in situ. Using stockpiling conveyors as part of a track mobile set-up is another perfect example of how-to cut-out unnecessary double handling, reducing fuel consumption and therefore carbon production.”
Powerscreen has evolved its product range to reduce environmental impact by making its crushing and screening equipment as fuel efficient as possible, using direct drive systems for its crushing range and improving engine capabilities and drive-line design for its screening range. Neil explains, “Direct drive systems are proven to be 13-18% more fuel efficient when compared with hydrostatic, resulting in significantly less carbon emissions, while improvements to our screening range has reduced engine speeds from 2,200rpm to 1,800rpm, which not only means cleaner engines with less emissions, but also reduced fuel usage and therefore carbon produced. For example, a typical mid-size screener running at 1,000 hours per year, has a fuel usage reduction of approximately 450 litres, which equates to 1.2 tonnes less of carbon produced annually.”
Another important tool for fuel efficiency is Powerscreen Pulse™, in-depth machine telematics that helps customers see how and where their machines are being operated, understand fuel consumption and carry out fault-finding activities to ensure optimised performance. Neil explains, “Powerscreen was the first mobile crushing and screening manufacturer to offer in-depth machine telematics with the launch of Powerscreen Pulse™ in 2013. In the early days, it generated a large volume of data, but now our system has been refined to deliver actionable information with customised reports and suggested actions for more fuel-efficient operation.”
Electrification is currently a key focus of the Powerscreen decarbonisation strategy. The Powerscreen Hybrid range, designed to give customers alternative energy options to operate their range of crushing, screening and conveying equipment, has been dramatically enhanced to include more fully electric crushers and screeners as well as models powered by innovative combinations of diesel and electricity. These options enable customers to choose which fuel to use, depending on cost, location and availability, and are of particular benefit to customers who operate in an area where electricity is more cost effective than diesel fuel, where diesel engine noise is unwanted or on sites where electricity is the preferred energy source.
Neil continues, “Customers using Powerscreen Hybrid units powered off the grid have been able to reduce onsite carbon emissions by 57% per tonne of material produced. While our hybrid customers have traditionally been in environmentally conscious countries and states, where legislation or financial incentives are more focused on green energy, we are witnessing a significant uptake in non-traditional locations, as customers prepare to comply with increased government drives for carbon neutrality.”
Powerscreen continues to spearhead the industry’s drive for decarbonisation and a clear demonstration of this is a brand-new concept for the future of crushing and screening—the Eco-Warrior™ battery powered screener. Working closely with automotive technology and using top of the range, hyper efficient drives and intelligent control systems, the Eco-Warrior battery powered screener has been designed to deliver on the powerful screening action that Powerscreen machines are famous for, while being a self-charging, or plug-in, model that features a simple, quiet engine with no after-treatment requirements. The required engine size has been cut in half compared with the diesel hydraulic unit and the battery pack can mean emission-free running or give a power boost.
Neil says, “To the best of our knowledge this is the first battery powered screener in the world and has been clocking up testing hours since it was built in 2019. It still delivers on the powerful screening action that Powerscreen machines are famous for and we are now exploring taking it from concept to mainstream.”
Concluding, Neil says, “This isn’t a publicity stunt; the drive for decarbonisation is real, with the UK, and other governments ruling that carbon emissions have to be reduced by 80% by 2050. It’s critical that we dramatically reduce our carbon footprint and Powerscreen has many solutions available today in support of this. However, we’re not stopping there—we’re taking it to the next level, continuing to be the pioneers in adopting technology that supports the industry in meeting the requirements of government decarbonisation laws—this is the future.”