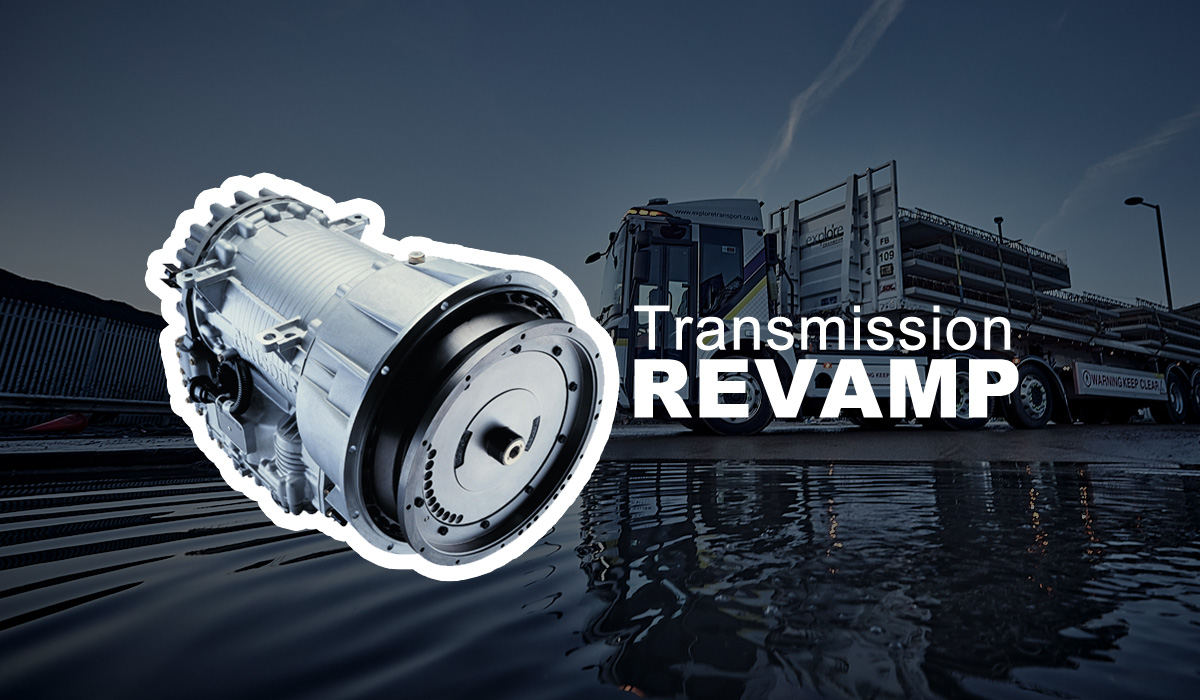
It’s time for construction fleets to consider whole life costs, says Nathan Wilson, account and area sales manager UK & Republic of Ireland for Allison Transmission.
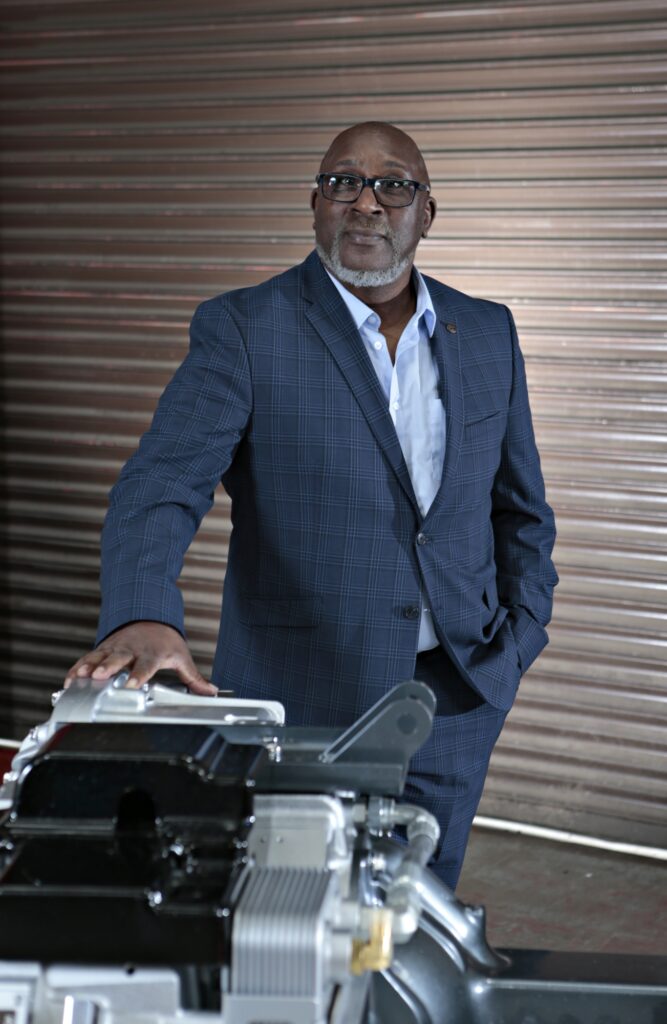
It’s no secret that tippers and other trucks targeted at the construction industry represent very good business for truck dealers. They probably suffer more minor damage and wear-and-tear than any other truck type and are guaranteed to keep workshops and parts departments busy almost from day one of their service lives.
Part of this is the inevitable rough-and-tumble of site work, but an often-ignored factor is that the automated manual transmissions (AMTs) which are now the standard offering from all the chassis manufacturers may not be ideally suited to the task at hand. The rigors of off-highway operation with ruts, steep inclines, and loose and slippery surfaces prove quite a challenge for the electronic systems that control the driveline, and this is evidenced by the ‘off-road’ setting available on some tippers that try to modulate the response of the transmission to rapidly changing amounts of variable grip by ‘holding’ gears in situations where the gearbox control would otherwise be ‘hunting’ between ratios.
But there is no denying that operations in these conditions place considerable stress on the weakest link in the powertrain: the mechanical clutch and its associated components.
Mechanical clutches are wearing components with finite lives: but they are also very vulnerable to premature failure once the wear process starts. The heat and dust generated by an over-stressed clutch do cumulative damage not just to the friction surfaces themselves but also to the clutch actuating mechanism and pressure plate.
An in-depth study of the engineering costs of a UK fleet’s industrial and commercial waste-collection vehicles has revealed a spate of expensive clutch failures on five different makes of trucks fitted with standard automated manual transmissions. Analysis using the fleet’s own internal maintenance and repair data revealed a 58% clutch failure rate on one premium make of vehicle equipped with the chassis manufacturer’s own AMT from 2020-2022, with the primary cause being thermal overload. Besides the clutch itself, other components requiring replacement after clutch failure often included flywheels and flywheel bolt sets, and clutch actuating forks and bearings.
The study found that the typical direct cost of fitting a replacement clutch at a manufacturer’s franchised workshop could be in the region of £3,000. Adding on related incidental costs, which can include vehicle recovery, downtime, and the hire of a specialist replacement vehicle, could see the cost more than double.
In the days of manual transmissions, such catastrophic failures were probably less usual. Driver abuse could be an issue, but skilled drivers were also aware of changes in clutch ‘feel’ caused by overheating, and could take appropriate action. This isn’t the case for modern ‘two-pedal’ trucks; where impending failure is not so apparent. The clutch works until it doesn’t, and then it needs to be replaced.
The fleet’s report also found repeated instances of clutch failures on the same vehicles over periods of five years or more, adding significantly to operational costs.
But there was one tranche of vehicles which experienced virtually no transmission failures at all. Although engaged in similar work to the rest of the fleet, these trucks had been equipped with factory-fitted fully-automatic Allison transmissions. The only issue reported with these was the replacement of a small number of electronic sensors. A quick and easy job compared to splitting a truck powertrain to replace a friction clutch.
Just like those Allison transmissions widely used in construction machines, Allison’s truck transmissions feature hydraulic torque convertors which absorb the loads imposed when heavily-laden vehicles have to traverse rough terrain. The stress of converting torque into motion is absorbed by the hydraulic fluid rather than turning into heat (and consequential wear and damage) as it does with a friction clutch.
So, why aren’t Allison transmissions more widely specified on construction trucks?
One reason is that there’s a stereotype that automatic transmissions make trucks less efficient because they ‘absorb power’. As a result, they have a reputation for only being suitable only for refuse or fire trucks.
This is absolutely not the case. The reality is that the torque converter boosts the effort imparted to the driving wheels beyond what would be possible with a friction clutch. Pressure accumulated in the torque-converter as the truck initially pulls away is turned into drive, giving a flywheel effect. With an AMT, excess torque is absorbed by the slipping clutch plate and turns to waste heat and wear.
Similarly, the seamless ‘power on’ shifting qualities of an Allison enable smooth and consistent ratio shifts, while an AMT will continuously experience power interruption during every shift change with a reduction of torque yet an increase of heat, eventually destroying its clutch. Allison transmissions are widely used in demanding performance-sensitive applications from fire appliances to Dakar rally trucks for this very reason.
This quality presents the truck buyer with two interesting fuel-saving opportunities without compromising performance. A higher final-drive gear-ratio can be specified: reducing fuel consumption and noise at highway speeds, or a smaller, lighter and less powerful engine can be chosen: saving fuel, weight and front-end cost.
On the subject of weight, Allison’s 3000 Series is the lightest transmission in the market, giving further opportunities to boost payload and productivity. With shift sequences controlled by software, individual transmissions can be fine-tuned for performance or fuel economy, and for operations in flat or hilly terrain.
Given the strength of this case, why aren’t more tippers, and other ‘vocational’ trucks, specified with fully automatics in the UK market?
Perhaps it’s time for all involved in the vehicle specification process to learn about different options and consider solutions that best suit end-users over the complete life of the vehicle. There is usually a price premium for specifying Allison transmissions over an in-house product, but the brutal truth is that this is likely to be less than the actual cost of a single failed mechanical clutch on an AMT.