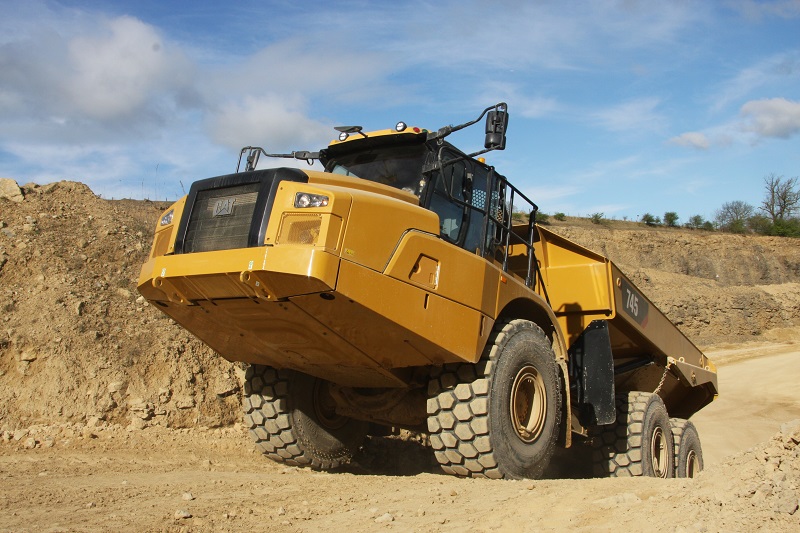
Nick Johnson checks out the latest version of Caterpillar’s 745 articulated dump truck which gains an all-new cab and big improvements to its operation.
With big UK infrastructure projects such as HS2 moving forward, the demand for the larger sizes of articulated dump trucks is set to rise dramatically. So the imminent introduction of a much-improved version of Caterpillar’s flagship 41.0 tonne (45.2 short ton) payload 6×6 ADT is well timed.
Caterpillar’s first 41.0 tonne payload ADT was the 745C which joined its other smaller articulated dump trucks in 2015. Now a newer version of the company’s flagship ADT will become available in July this year. But, rather than being designated the 745D, it will just be known simply as the 745.
In the past, Caterpillar has marked major product improvements by adding the next letter in the alphabet after the model number – with intermediate updates being labelled series 2.
This logic is now history as the new Cat 745 articulated truck represents the first machine featuring a new Caterpillar model numbering system, which departs from the previous alphanumeric style. So new Cats will have a numeric-only coding system.
The world source for Cat ADTs is the company’s big factory in Peterlee, County Durham. This facility includes not only the production lines but also the design engineering and product support departments for these machines.
And to aid the development, testing and demonstration of new ADTs, the company has a dedicated ADT proving ground near to the factory.
Situated in an old quarry, the Caterpillar ADT Proving Ground was the ideal place to inspect and try out the new 745. Putting the newcomer alongside a current 745C quickly revealed the big different between the two machines – the all-new cab design.
The distinctive new cab on the latest 745 has been completely re-engineered from the inside out using global operator feedback to advance comfort and ease of operation.
It incorporates a new external “spinal” ROPS structure which boasts bonded rear quarter glass. This design eliminates the previous rear structural corner pillars to give the operator a dramatic improvement in rear quarter visibility when reversing.
The new cab is much wider than its predecessor and overall its internal volume has increased by 20% so it feels much more spacious. All the glass is flat except for the slightly curved front screen.
With at least 25% more glass in the sides of the new cab, one could be forgiven for worrying about sitting in a ‘hot house’ during very warm weather. But the Cat engineers have ensured that this does not happen by using infrared reflective glass all round to reduce the solar heat loading to the cab interior by 20%.
There are also see-through roller style sun blinds on the rear and side windows.
Also contributing to a comfortable operating environment is the machine’s improved climate control system with 12% more airflow. Complete with additional vents, the system allows the operator to select his desired working temperature.
As well as a sliding window on the right, the new cab also gains a sliding top window in the cab door. This addition can provide extra fresh air ventilation and can make it easier to hear the horn of the loading machine.
The 745 operator will appreciate the new heated and cooled seat (with more adjustments) which comes as standard for UK customers. There is a seat belt indicator and an operator presence switch to remind the operator to wear his seat belt.
A major in-cab improvement that will really please the occupant is the dramatic reduction in internal noise level from 79dB to only 72dB. This very noticeable quietness has been cleverly achieved by using better sound insulation.
Details can make a big difference to an operator’s perception of a machine and the new Cat should please by now providing a large side storage box that can be conveniently cooled or heated by the machine’s heating, ventilation and air conditioning system.
Other practical features that will be appreciated by the operator include twin cup holders, hooks for coat and hard hat and smaller storage pockets for mobile phones etc.
Getting up into the cab has been made easier with the addition of a new rear grab rail. A good addition is a switch inside a panel on the nearside front fender to turn on the new access light above the steps to aid entry in the dark.
This switch also initiates machine displays and checks. The access lights also come on for around a minute when the cab down is opened to allow a safe exit from the machine after dark.
Another aid to entry and exit is the use of a new pressed door that weighs 36% less than the fabricated door used on the previous 745C. Designed to be both light and strong, it has a gas strut to assist opening and closing and there is also improved sealing against dust.
When driving the machine, the operator gets visibility benefits from the addition of a new external mirror above the centre of the screen as well the redesigned side mirrors.
Now rather than being attached to the handrails, the side mirrors connected directly to the cab structure which means there is less vibration to distort the rear view from them when traversing rough ground.
The new side mirror design has resulted in a useful reduction in operating width from 4,166mm to 3,802mm. This change gave me more confidence when driving the fully loaded ADT through the narrow concrete tunnel under the A1 that connects the two sides of the extensive Caterpillar Proving Ground.
The side mirrors swing in for road transport and the exhaust stack is now lower so that overall height has conveniently gone down from 4,084mm to 3,762mm. This means that the exhaust stack does not have to be removed for road transport.
The new 745 operator gets a new touch screen display with revised menus and more intuitive input control. It is easier to monitor and configure many machine options. And, with more pixels for better resolution, the display is clearer – especially the view displayed from the rear facing when the machine is reversing.
The really big change with the controls is the replacement of the former separate transmission and hoist (tipping) lever by a single multipurpose lever that also controls the new Assisted Hoist Control feature. The new lever provides intuitive, one-handed control of the parking brake, travel direction and gears as well as the body hoist.
The new lever has two yellow buttons on its nearside. These buttons allow the convenient control of the machine’s speed limiter and transmission hold/waiting brake.
The integral control for the the new Assisted Hoist Control activates an automated sequence which effectively reduces the steps needed to reverse the truck and tip its load from 13 to 7.
This system automatically neutralises the transmission, applies the waiting brake and raises the body to maximum discharge angle at high engine rpm. Whilst tipping can still be carried out manually, the automated control saves time and makes it much simpler for the operator.
A new safety aid during both tipping and travel over rough ground is the Cat Detect with Stability Assist system. Visual and audible warnings are given to the 745 operator if his machine is approaching an unsafe angle during operation.
The visual display has graphics that clearly the show the grade and the stability of the front and rear portions of the ADT with orange pointers that move from central green ‘safe’ sectors to grey ‘danger’ areas on either side when the machine is on side slopes. If the pre-set maximum safe angle is detected, and an orange pointer goes into a grey sector, the operator will not be able to tip the load using the automated Assisted Hoist Control.
Another safety improvement is the new emergency stop brake. This prominent red button provides extra reassurance that trouble can be avoided in the unlikely event of issues with both the main and secondary brake circuits.
A simple but effective aid to safely loading the 745 are the new Load Status Lights. Pairs of red and green lights are now prominent on the four corners of the new cab. Using the sensors used by the Cat Production Measurement system these lights allow the operator of the loading machine to clearly see when the rated payload is being reached.
This helps to maximise every payload and therefore productivity, while minimising the possibility of overloading and the premature wear it can cause.
During operation the operator can select a new Economy Mode which automatically changes the gear shift points to provide, it is claimed a fuel saving of around 5% on average.
In applications where the 745 is not required to operate at full productivity, use of the Economy Mode results in upshifts being made a little bit earlier and downshifts a little bit later so as to avoid high rpm peaks.
The 745 retains the same 375kW (504hp) Cat C18 ACERT engine as its predecessor as well as the automatic traction and retarder controls. A change to the automatic traction control is that it is now proactive rather than reactive.
Like all the other Cat ADTs, the new 745 will be made at Caterpillar’s big factory at Peterlee. This facility was established by the entrepreneurial engineer David Brown who introduced his first DJD D250 articulated dump truck utilising Cat engine, transmission and axles back in 1974. Caterpillar acquired the DJB design rights in 1985 and subsequently bought the company and the manufacturing facility.
The DJB era is remembered by the display of an historic DJB D35 ADT outside the Peterlee factory. The continued production of ADTs on this big site and the introduction of the improved 745 should help Caterpillar and its UK dealer Finning to better compete for the volume business that should result from the start of major infrastructure projects such as HS2 – particularly if Made in Britain becomes a more significant factor in the wake of Brexit.
For more information on CAT click here.