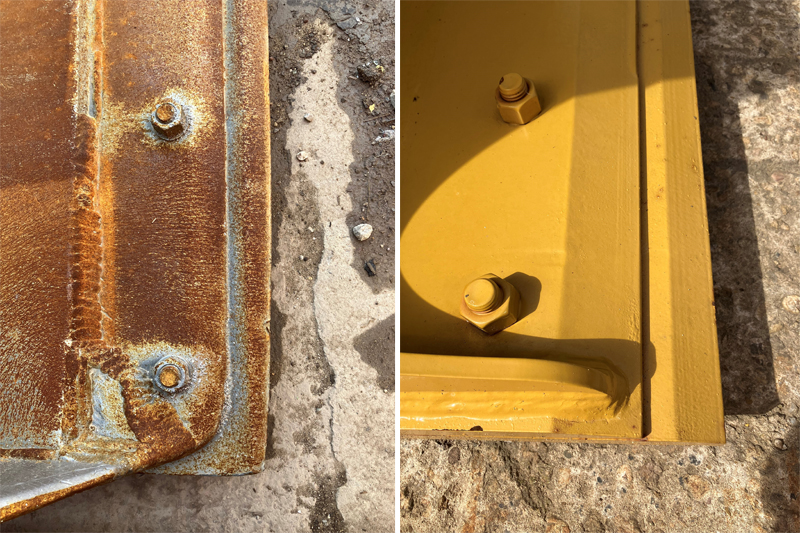
CPN caught up with Cheryl Griffith, wear parts product manager at Finning, to get her expert view on selecting the right type of tip and what signs to look for when it comes to replacing them.
Inspecting and replacing bucket tips regularly is essential to avoid machine damage while maximising its output. However, it’s important to match the right tool to both the machine and the work it is doing to optimise performance and machine longevity.
Work tools are an important part of any machine. Not only do the tools protect the most expensive machine components, but they also have a direct effect on the productivity, fuel consumption and maintenance costs of your machine. Choosing the right tips at the right time, enables operators to achieve the lowest cost per tonne, whilst also safeguarding the engine and powertrain life of your machine.
These tools have a direct effect on the machine’s ability to perform effectively. A worn out work tool can also increase operator fatigue, for example an increase in cab vibration caused by resistance on the system, means it takes more time to move material, as worn tips lead to less penetration into the pile.
Warning signs
One of the biggest issues we see is when customers don’t have any planned maintenance programmes in place. These are really important as they flag up potential issues with a machine before they become a serious problem.
Checking your bucket tips regularly as part of a wider check of all your wear components is essential. The kind of environment the machine is working in affects the rate of wear, for example, if a machine is operating in a quarry and working with granite, which is an incredibly hard material, the bucket tips will wear at a quicker rate.
Visual checks and what to look for:
- excessive wear on bucket tips – tips worn through on the bottom or cracked in the pocket area should be replaced.
- damage to the bucket tip adapters – badly worn bottom straps worn into the bottom cavity should be replaced.
- damaged or missing retainer pins – tap lightly on each pin and if it moves easily replace the retainer.
- cracks on the base edges beside adapters and corner welds.
- cracks on base edges on the top and bottom of the rear weld.
Generally, the tip should look like a triangle shape to the side, but if the tip has a blunt end rather than a sharp end it can really affect the efficiency and impact of the digging process. This means you get less penetration, less efficiency, and it’s not possible to get the full force of the machine into the load to lift the maximum capacity.
Another thing to check is that you can shake the tip as there should be some play in it rather than it being completely rigid. However, if there’s too much play in the tip, this means the adapter is starting to wear and will make the machine less efficient and reduce tip retention.
When a tip is wearing it can also mean the fuel burn will increase because the machine is having to work harder to break up the same material. This leads to wear to the adapter at the back of the tip, which is why not replacing tips regularly can quickly escalate machine costs as these are more expensive to replace.
The next part to be affected is the bucket – the most expensive wear part to replace as it’s such a large piece of steel – but this should last for a much longer period in comparison if wear protection is used properly.
Tip types
The tip sits onto your adapter, which should last twice the length of time as the tip on average, if the tip is replaced more regularly.
The shape and thickness of the tip you chose is also important. It should it be compatible with the machine it is being fitted to but also to the task it is carrying out and the nature of the material being worked.
As a rule, tips are generally designed to be either low impact, to deal with something like limestone granules for example, low abrasion as in topsoil, high impact where a machine will be working at the quarry face moving big boulders, or high abrasion where a machine may be working consistently in sand.
Tips also come in several product types. For Cat machines the tips range from ‘General Duty’ (a lower price solution without compromising on quality) to the J Series, K Series, and premium Advansys which are typically used in high productivity applications on larger machines because they have more wear material and an engineered profile. Within Advansys there are different tip types ranging from penetration plus to heavy duty and high abrasion.
Competition time!
CPN has teamed up with Finning to offer 25 lucky readers the opportunity to get your hands on a fantastic CAT-branded work cap.
Click here for your chance to win and answer the following question:
What is the name of Cat’s premium range of tips?
- Advantix
- Advantage
- Advansys
Deadline for entries is May 31st, 2024. Terms and conditions apply. See website for details.