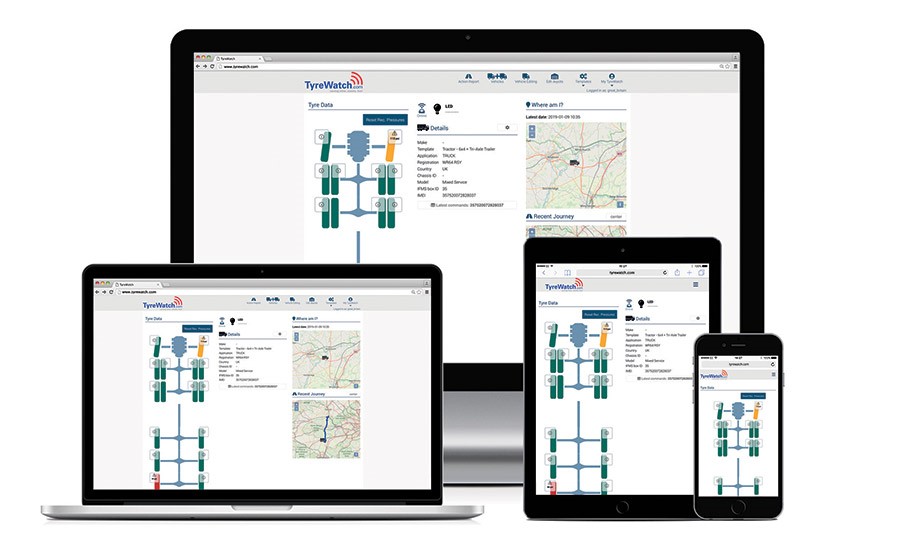
The quarry sector is looking to TyreWatch for improved safety and cost control
Principle considerations for quarry operators are health and safety, and efficient materials extraction. Given the potentially dangerous working environment, the need for strict safety procedures is paramount – not only to protect personnel but also to help maintain production levels.
TyreWatch maintains its remote monitoring and control systems dovetail perfectly with these essential requirements, particularly as under-inflated heavy equipment tyres cannot always be determined by visual inspection alone.
Large earthmoving tyres can run under-inflated for weeks, which causes the tyre to over flex. This, in turn, causes the tyre to wear faster, the rim components to suffer premature damage and the potential for a serious incident to be ever present. Moreover, it is a well-known fact that under-inflation leads to shortened tyre tread lifespans and can make the tyre casing at the end of its first tread life unsuitable for remoulding.
TyreWatch Sales and Field Technical Manager, Peter Roffey explains: “Running underinflated tyres leads to overheating and potential blow-outs which inevitably puts site operatives at risk. Connect this with the extensive paperwork required to comply with the HSE’s RIDDOR directive (Reporting of Injuries, Diseases and Dangerous Occurrences Regulation) and there is a perfect case for the TyreWatch system to ensure all-round safety and adherence to the law.”
Roffey explains that its customers are increasingly requesting tyre pressure and temperature data for their connected machines to improve onsite working practices and thereby embedding remote monitoring into their core operating systems. A current example can be seen with Imerys, a market-leading supplier of mineral-based solutions, who report significant reduction in tyre replacement and vehicle downtime since installing a TyreWatch remote monitoring service at its quarry in Furzebrook, Dorset.
With a mixed fleet of off-road heavy plant and six bulk tippers, Imerys were looking for a solution to combat problems associated with tyre-pressure loss and, following a recommendation, turned to the company’s PlantSmart telematics system.
“In former times,” explains Quarry Supervisor, James Johnson, “we might have no idea if a certain tyre was losing pressure or failing, so with no opportunity to resolve the problem we would have to take vehicles out of service and make emergency tyre replacements. This not only interrupted workflow but also presented a potential safety hazard.”
Having this type of connected solution is the safe way forwards to alert quarry operators to attend to tyre pressures in good time and, accordingly, the system delivers maintenance and warning notifications before the tyres reach a critical pressure. This allows the machines to carry on working with tyre repairs being planned in for the end of the day or during a driver rest period.
Using the automatically captured data also helps operators to look at site trends for tyre temperature peaks: large earthmover tyres heat up, and take a long time to cool down, so real time temperature records can help to reduce tyre overheat, which prevents loss of tyre service life, improves safety and reduces cost.
“The best outcome for all quarry operators and owners” adds Peter Roffey, “is to invest in a connected system that simultaneously notifies the quarry management, maintenance teams and – by cab alert – machine operators of every low tyre pressure event.”
Roffey says that while TPMS is by no means a new concept, its telematics monitoring system takes it a step further by making sure all issues are monitored in real-time without the need to solely rely on the driver or later visual inspections – which could be too late. The added benefit to the operator is paperless, digital reporting which can be instantly accessed for all compliance checks and inspections.
“We use the direct TPMS on our quarry-based vehicles with high pressure tyres, while on the loading shovels, a pit tractor and our bulk tippers we use the IoT (Internet of things) remote system – which also provides temperature monitoring.” This, says James, is useful to detect any sudden temperature increases, which could indicate a binding brake, hub failure, damaged suspension, or incorrect wheel alignment.”
In addition to the in-cab alarm system, automatic alerts are sent to designated email addresses within the Imerys team, notifying them of any events as they occur and automatically updating as the problem develops. According to James, by never running an underinflated tyre, Imerys are permanently saving on fuel and maintenance costs. Furthermore, by greatly reducing particulate emissions from tyre tread abrasion, the company is also helping to minimise its environmental impact.
“We’ve saved many tyres using TyreWatch,” concludes James Johnson, “and the safety and environmental aspects are far-reaching. We have certainly embraced the benefits of predictive tyre management, and I’m pleased to say, so too have all of our quarry transport contractors.”