Total cost of ownership depends on far more than the design and quality of a machine. Utilisation and operation are major contributors to profitability. Here are three tools all Volvo customers have at their disposal to dramatically reduce their running costs.
1. Insight Reports
Volvo’s Insight Reports – comprising Fuel Efficiency Reports, Health Reports and Summary Reports – make light work of interpreting complex telematics data and help customers to actually use this information to improve their TCO. Compiled for individual machines or an entire fleet, the reports provide an overview of fuel consumption, utilisation, machine alarms and operating behaviour. Customers can see at a glance the actual payback they are getting from their machines and use the insights to agree on tangible actions for improvements.
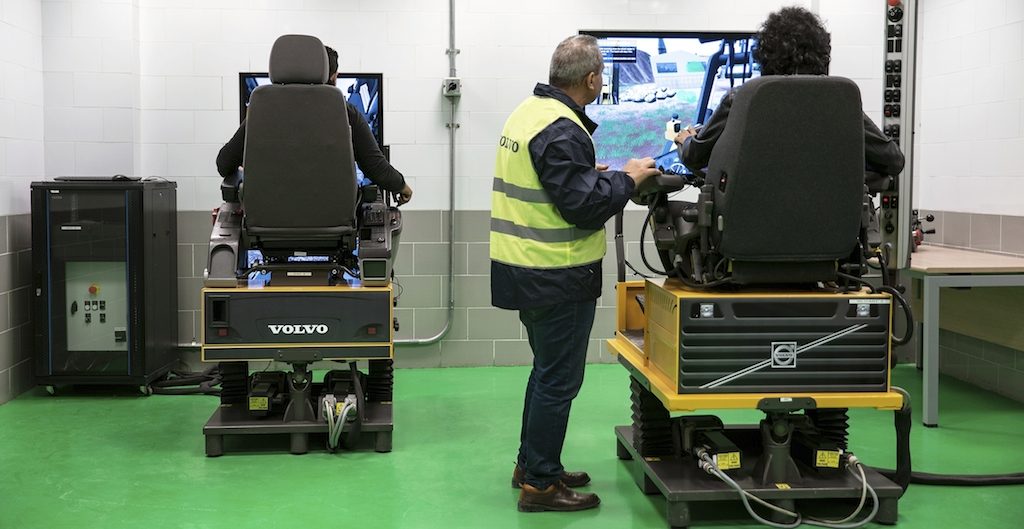
2. SiteSim
SiteSim calculates the optimum set-up for a customer’s site to minimise waiting or idling and give the lowest possible total cost of ownership. By inputting the type of material, distance from the loading to dumping points, and topography of the site (thanks to 3D drone measurements and photos), Volvo CE can recommend the ideal number and capacity of machines, as well as the optimum routes operators should drive, based on the tonnes per hour and the cost per tonnes. Site studies such as this are regularly carried out in the mining industry, but Volvo CE is unique in its ability to offer comprehensive simulations for small and medium-sized sites too.
3. Operator training
Volvo CE and its dealers offer customers a variety of training solutions to ensure operators are working in the safest, most efficient and productive way possible. Even experienced operators benefit from training as they learn how to use all the latest Volvo features to full advantage. Customers who invest in operator training soon recoup their investment, thanks to savings on fuel, increased overall production and reduced maintenance expenses. After that, it all adds to the bottom line.