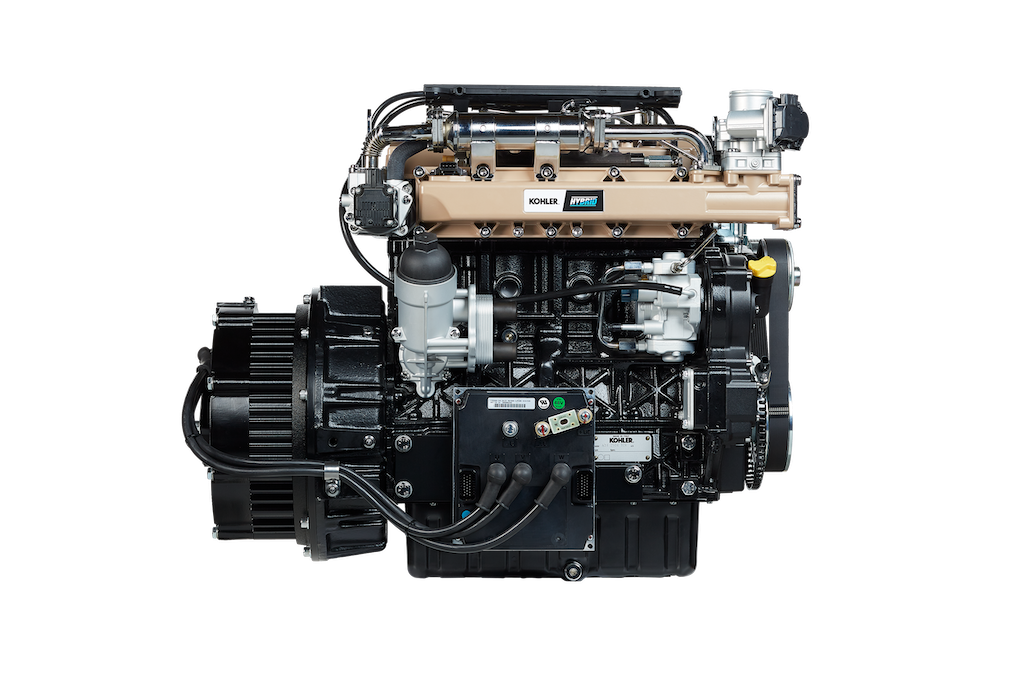
K-HEM Series makes its debut with the model K-HEM 1003 on board of the aerial working platform Spyder DT28 by Cela at the 8th edition of GIS Expo, the Italian trade show for lifting, handling and heavy transport experts.
The aerial working platform Spyder DT28 is the outcome of a fruitful collaboration with Cela that has seized the oppurtunity offered by the features of the hybrid unit K-HEM 1003, that perfectly fits the needs of such a machine.
“Always focused on uncompromised innovation and the development of new technologies capable of making our products unique, we are convinced that this is the first step of a long path aimed at reaching increasingly ambitious targets” said Paolo Troni, CEO at Cela.
The internal combustion engine doesn’t require aftertreatment systems. Therefore, the machine’s downtime caused by the regeneration process has been totally eliminated. The electric unit allows for reaching high peaks of power required by the machine, thus guaranteeing a high level of productivity.
“The aerial working platform Spyder DT28 is the perfect example of the power to work together: it represents the outcome of a complete integration between the hybrid unit and the machine aimed at maximizing productivity and minimizing the battery pack size” declared Massimiliano Bonanni, General Manager – Product Strategy at Kohler Engines.
K-HEM Series, the age of rightsizing
Kohler is an alternative player, going against the flow with respect to traditional engines and responding to the new demands of a constantly changing market for solutions that are more dynamic and flexible and greater focus on what customers really need. Our aim is to facilitate the job of constructors by improving the performance of their machinery. In order to do this, we offer them our support so they choose the best solution for their needs: by expanding its range of hybrid solutions, Kohler aims to ensure everyone can choose the best engine for their application.
Electrification refers to the design of a system running on electricity: in the construction industry, these can be hybrid systems or purely electrical systems. In the panorama of hybrid solutions, there is also a distinction to be made between hybrid in series and hybrid in parallel: a hybrid system in series simply converts chemical energy into mechanical energy, and this
is converted in turn into electrical energy. A parallel hybrid system can deliver mechanical energy, coming from chemical energy, at the same time as it delivers electrical energy, coming from a previously-charged battery pack. This offers the advantage of using mechanical and electrical energy simultaneously. The combination of the two types of energy is the main pluspoint of any parallel hybrid system.
The range of K-HEM hybrid units is based on the concept of a parallel hybrid system: this enables constructors to fit K-HEM units onto the hydraulic system of their applications, just like they used to do with endothermic engines.
Later, when they decide to re-engineer their machines in order to exploit the full benefit of running applications on electrical power, our engineers will be ready to support them step by step to design increasingly efficient machines.
Kohler does not intend to drive the process of electrification at all cost, but is committed
to exploiting the potential of every source of energy in order to reach a truly optimised performance of applications based on operating cycles. As a result, Kohler’s strategy is to extend its range of hybrid solutions.
After analysing the market case by case, we realised there is a series of applications fitted with over-dimensioned engines for specific features. Their operating cycles do not need all the power that the engine is capable of delivering, or does not need it all of the time. Consequently, we identified two thresholds that are particularly interesting: 19 kW, i.e. the limit for Stage V legislation’s requirement for the use of DPF, and 56 kW above which the same legislation also requires the use of SCR.
In order to offer an alternative solution capable of tapping on these two power nodes, the new K-HEM 2504 runs alongside the K-HEM 1003: the K-HEM 2504 is a hybrid unit generating a combination of electrical and mechanical power consisting of a KDI 2504TCR 55.4 kW diesel engine that complies with Stage V legislation and is without SCR, and a 48 Volt electric motor that guarantees 19.5 kW peak power and 9 kW continued power, and maximum safety levels due to the voltage. The new K-HEM 2504 hybrid unit offers even more efficient DPF management making the regeneration processes fully transparent for the end user, as it is possible to exploit the temperatures reached to recharge the battery pack.
The modern and advanced DNA of the KOHLER KDI 2504TCR engine makes it the perfect partner for an electrical unit: KDI engines deliver a very high performance and the combination with electrical power can equal, if not exceed, the performance offered by higher spec engines in terms of horsepower, as well as a smaller footprint.
Our hybrid solutions are not designed to offer a simple downsizing, but to be part of a broader concept of the rightsizing of applications, namely choosing the right size: the most suitable size for each specific application. Kohler offers constructors a full range up to 105 kW, which investigates different sources of energy that are increasing and diversifying as time goes by.
Hybrid solutions not only save OEMs the complexity of post-processing systems and add extra power, they also offer a range of possibilities. They can simply replace an endothermic engine without worrying about installation problems because K-HEM units have the same integration with the hydraulic system or with the mechanical transmission as a diesel engine. Otherwise, the application can be re-engineered in order to make it more efficient: the current generated by the electric motor can run a series of actuators and guarantee more punctual and optimised management, leading to improved machine performance as a whole.
K-HEM Series units allow excavators to have faster and more precise movements compared to the past, with improved efficiency and productivity. Or they make sure aerial platforms exploit the availability of electricity when peak power is required and then use the diesel engine as standard for cycles operating at low speeds. For the same reasons, we believe K-HEM Series units are a perfect match for applications like welding equipment, forklift trucks, telescopic lifting equipment, tyre- or track excavators, chip grinders, and cable tensioners. K-HEM Series units hybrid units guarantee the general optimisation of machines and the possibility to store surplus energy in the batteries to be delivered when needed, drastically reducing running costs; the applications will enjoy the inherent flexibility of parallel hybrid systems, namely the possibility to run on mechanical energy, on mechanical energy plus electrical energy, or with electrical energy alone, soon available for the K-HEM Series.
KOHLER presents K-HEM 1003
In light of the changes that the new emissions directive has brought to the off-road applications sector beginning on 1 January 2019, Kohler has added a product to its array that is capable of meeting the new needs of equipment manufacturers in this sector. A variety of energy sources are available on the market. Rather than investigate their different applications and individual characteristics in order to set them up in competition with each other, Kohler has chosen to integrate them, to pair them with each other, so as to reap all of their potential value.
This is the philosophy behind K-HEM 1003, the unit that generates power using a combination of a KDW 1003 18-kW diesel engine, compliant with Stage V standards and without DPF,
and a 48-volt electric engine that guarantees 15 kW of peak power and 9 kW of continuous power. This means that the unit is capable of providing over 30 kW without the need for exhaust-gas aftertreatment systems. What’s more, K-HEM can operate as a generator for energy accumulation systems.
The features that the K-HEM hybrid unit offers have been designed to satisfy the needs of all those types of equipment that are distinguished by intermittent duty operation cycles that call for power peaks (welders, mowers, tractors with implements, etc.) and machines that chiefly run continuous low load operation cycles, which prevent them from reaching the temperatures necessary for passive regeneration to occur inside the particulate filter (aerial platforms, forklifts, etc.).
With K-HEM, the power base is provided by the combustion engine, while the power peaks are guaranteed by the electric engine. This system, which complies with the limits laid down in Stage V standards, makes it possible for machines to avoid derating and guarantees high productivity levels. Indeed, the built-in master control unit allows users to monitor and manage working modes and transitions based on their needs.
All of this translates into lighter, more compact and better-performing machines than in the past, capable of exploiting all of the benefits arising from the integration of mechanical power and electric power: less complex engines; an absence of aftertreatment systems; the ability to store and use excess energy produced thanks to the built-in alternator; energy recovery during braking and exhaust phases; the ability to manage operations using the master control unit; reduction of gas emission, noise and consumption rates; improved performance and power modulation, thanks to the integrated management of each operation.
Greater efficiency. The diesel engine guarantees maximum performance in specific operating conditions. This means that the hybrid unit makes it possible to achieve optimal operating points more rapidly and more frequently, thereby increasing the efficiency of the operations performed and, consequently, the equipment’s productivity.
Recovery operations. Thanks to the dual function of the electric component, which works both as a generator and as an auxiliary engine, it is possible to recover energy from the transmission system during the machine’s braking and exhaust phases and from the combustion engine itself during operating phases with low energy demands. The energy stored in the battery will thus be available when the machine requires more than the threshold of 18 thermal kW of installed power, exceeding even 30 kW. This translates into considerable savings in terms of emissions, consumption and installed thermal power.
Perfect integration. Equipment manufacturers do not need to worry about possible installation problems, given that the hybrid unit can be integrated into a hydraulic system or a mechanical transmission, in the same way as a diesel engine.
Precise management. The high degree of integration between the mechanical and hydraulic parts that the hybrid unit allows makes it possible to completely optimise machine management: each actuator can be managed by the hydraulic or electrical system depending on specific requirements, and controlled by the master control unit that oversees the system. The most striking example is that of agricultural attachments: the ability to disengage them from the mechanical system and manage them using the electrical system now allows for exceptional optimisation of operations.